Keywords
Abstract
The development of atom-economical and efficient processes for obtaining a variety of chemical products using CO2 as C1-synthon plays an increasingly important role in modern scientific and technological research. Due to the inertness of CO2 many extremely attractive routes to valuable chemical products turn out to be impossible to implement, particularly for thermodynamic reasons, leaving one only dreaming about them as something unattainable. This review demonstrates how the catalytic coupling of ethylene and CO2 into acrylic acid, once considered a "dream reaction" has not only become a reality, but has also evolved into the category of technological processes. The key stages of the long-term development of this unique reaction from the discovery of metal activation of CO2 and stoichiometric preparation of metallalactones to catalytic synthesis using a variety of metal-catalysts (Ni, Pd, Ru, Rh) showcase the ingenuity and skill of researchers as well as an example of consistent development in this field of chemistry. We believe that this remarkably successful example will inspire scientists to tackle any "impossible" problems.
The bibliography includes 117 references.
1. Introduction
Acrylic acid (AA), CH2=CHCO2H is the first representative of α,β-unsaturated carboxylic acids. Anhydrous (glacial) AA is a colorless liquid with a boiling point of 141.0 °C and a melting point of 13.5 °C. In terms of acidity, AA is slightly stronger than acetic acid with a dissociation constant of 5.5 × 10–5 (pKa 4.26). It is completely miscible with water and has the lowest freezing point of –12.5 °C with 37% water content. In chemical properties, AA is similar to both carboxylic acids and unsaturated compounds, displaying a significant ability to polymerize. Due to this, the surface liquid where the polymerization inhibitor (phenothiazine, hydroquinone or its monomethyl ester) is concentrated must not be removed from the solidified AA and the solidified acid must not be heated above 30 °C[1].
Despite its high chemical activity, AA causes little harm to the environment and living organisms. Additionally, AA is a biodegradable compound that degrades rapidly in light, soil and water. Apparently, due to this, AA is rare in nature. It is known to be produced by seaweeds and has also been found in the rumen (first stomach) fluid of sheep.
As a member of an important class of carboxylic acids, AA has high relative content of carbon dioxide, up to 61% of the gross weight of the AA molecule. It serves as an excellent example of efficient CO2 utilization. Notably, among various products of organic synthesis obtained from CO2, organic acids such as formic acid, hydroxybenzoic acids, adipic acid, etc. constitute a significant part (Figure 1)[2-16]. Additionally, CO2 has several advantages as a reagent, including its affordability, non-flammability, non-toxicity, widespread availability and inexhaustibility as a main component of industrial gases used in chemical production, thermal and power plants, etc. and as a constituent of air (> 0.04%). The tools for reactions with CO2 is constantly expanding to include a wide range of catalytic, photocatalytic and electrochemical methods[17]. This field of chemistry is progressing rapidly, with new CO2 carboxylation methods that do not even require special equipment and can operate at normal pressure and temperature. In addition to the obvious advantages of this C1-synthon (see Figure 1), there is another powerful incentive for its use in industrial synthesis.
As the primary greenhouse gas in the atmosphere, CO2 is responsible for ongoing global climate change and the resulting negative impacts on human life[18-20]. The implementation of the 2015 Paris Climate Agreement, which aims to reduce CO2 emissions, requires a fundamental restructuring of the technological sector. Energy-efficient, atom-efficient processes based on CO2 recycling will be crucial in this transition. In this technological paradigm, precise control over the amount of CO2 emitted is a key factor that defines the quality of the technology and even the products themselves.
The proposed methodology for estimating emitted CO2 includes not only the production stages, but also the entire ‘life cycle’ of the product, including its processing and decomposition as waste[6]. Creating products with high CO2 content is undoubtedly relevant and economically feasible. However, achieving this goal is challenging because many chemical transformations of CO2 are thermodynamically prohibited. This is due to the high stability of the carbon dioxide molecule, which in the potential energy well is located much lower than other compounds (ΔGR0 = –396 kJ mol–1). Similar to the water molecule, it is the most stable product of combustion and oxidation processes[2]. Consequently, the Gibbs energy of many of its reactions turns out to be positive, primarily due to the energy costs of CO2 activation and changes in the degree of oxidation of carbon atom.
Based on CO2 and other small molecules, one can envision several highly atom-efficient pathways for synthesizing compounds of great value to industry. However, these pathways may be thermodynamically or due to other energy factors or technologically unattainable. In this case such processes are often referred to as ‘dream reactions’ because they are highly desirable yet challenging to achieve. Examples of ‘dream reactions’ include the synthesis of methanol by direct oxidation of methane, where the problem of selectivity is of fundamental importance, because methanol oxidizes much easier than the starting methane (Scheme 1). CO2 endothermic syntheses of formic acid (ΔGR0 = +32.9 kJ mol–1), acetic acid (ΔGR0 = +55.0 kJ mol–1), adipic acid (ΔGR0 = +77.4 kJ mol–1), dimethyl carbonate (ΔGR0 = +26.2 kJ mol–1), phenylisocyanate (ΔGR0 = +306.6 kJ mol–1), and other aryl derivatives are also considered ‘dream reactions’. These reactions require a combination of special approaches, to alter the thermodynamics of the process and significantly increase their rate.
Therefore, the most important role in the implementation of such transformations is assigned to catalytic systems. Although they do not change the thermodynamics of the process, they allow for lowering the energy barrier, thus, opening the possibility of more effectively controlling the chemical equilibrium and shifting it toward the reaction products. In particular, in the catalytic synthesis of formic acid, its conversion to the solvated salt form allowed for making the process not only thermodynamically favorable but also catalytically efficient with TON values reaching several million[21, 22].
Among the ‘dream reactions’ (see Scheme 1), the synthesis of AA holds a special significance and a revealing history, from the initial idea to the testing of the technological scheme of synthesis in a laboratory. Several scientific groups have achieved remarkable success in implementing this challenging reaction[23-27], although one step still separates researchers from turning the dream into reality. Given this, each of us can contribute to taking this important step by combining the achievements of many chemists to improve this breakthrough reaction and create an efficient industrial technology based on it. Therefore, this paper will analyze the most important stages in the development of this process and the existing obstacles that complicate the transition to an efficient industrial synthesis of AA.
AA is an important industrial product, as evidenced by its impressive global production forecasted at 7.8 million tons in 2024. Derivatives of AA such as esters and salts as well as polymers based on it are widely used in various industries and households. These derivatives are utilized in coatings, paints, superabsorbents, adhesives, sealants, polymer fibers (such as Acrilan, Creslan, Dralon, Vonnel, etc.), components for 3D printing, reagents for oil production, water purification and more.1 Thanks to the ease of radical poly- and copolymerization, a wide variety of acrylic polymers can be achieved by using different types of initiating systems. The choice of the type of ether radical controls the degree of polymer adhesion or fiber smoothness. Polyacrylates hardly ever yellow in direct sunlight because they absorb UV radiation below 290 nm. Copolymers of acrylate ester and methacrylate ester (‘pure acrylates’) have excellent UV light resistance, making them ideal binders for transparent coatings with low pigment content, which is among the important advantages of polyacrylates[28]. Acrylic fibers are also a major source for pyrolysis into carbon fiber[29]. Water-soluble polyacrylic acid and its salts with a molecular weight of 2 – 5 thousand are utilized as deposit inhibitors, sludge dispersants in cooling water systems, pigments or paper coating materials[30]. Copolymers with a small number of hydrophobic side groups are also useful as fracturing fluids in oil drilling[31]. Cross-linked sodium polyacrylate is a common absorbent in baby and adult diapers[32-34], feminine hygiene products[35]. It should be noted that the market share of sodium (poly)acrylate involved in the production of superabsorbents[36] reaches 70% and is an important component of the total volume of AA produced. Cross-linked polymers of acrylic or methacrylic acid neutralized to more than 50 mol.% are also used to provide high water retention capacity and viscosity of gypsum[37]. The cross-linked water-absorbing AA polymer is integrated into the formulations of prolonged-acting tablets[38]. A mixture of water swelling particles of anionic AA polymer or methacrylic acid and their soluble salts and cationic aminoacrylate and aminoalkylacrylamide polymers are used in precoated adhesives for wallpapers[39].
2. Industrial processes for the production of AA
Given the demand for acrylate derivatives, several industrial processes have been developed for AA production. In 1945 Walter Reppe first developed the process of stoichiometric alkoxy(hydroxy)hydrocarbonylation of acetylene using nickel carbonyl (Scheme 2)[40]. A quarter mole of nickel carbonyl was added dropwise to an acetylene-saturated alcoholic or aqueous solution containing 0.5 equiv. of HCl under normal pressure to produce ethyl acrylate or AA in 80% yield. However, this method of conducting the process is not suitable for industrial synthesis due to the release of explosive hydrogen, difficulty of regeneration of Ni(CO)4 and its high toxicity. Despite these limitations, it laid the foundation for a more efficient method. It was discovered that introducing CO (up to 2 bar) into the reaction could significantly reduce the toxic nickel carbonyl loading, and a method for its regeneration via ammoniacate was developed. This modernized process was utilized by Rohm & Haas and Toagosei to produce methyl acrylate[41]. Later, Reppe and Stadler (BASF) developed a catalytic method for the synthesis of AA. This method involved carrying out the reaction under pressure with a mixture of acetylene and CO (1 : 1) at 170 – 220 °C in the presence of nickel(II) and copper(II) halides[42].
The ketene method was successfully used in the synthesis of AA and its esters (Scheme 3). Ketene is formed by cracking acetic acid or acetone and then reacts with formaldehyde to produce β-propiolactone. The β-propiolactone is subsequently subjected to alcoholysis or hydrolysis in the presence of sulfuric acid. The intermediate β-hydroxy-derivative is dehydrated to form AA or its ester[41]. This method, although historically significant, is not commonly employed due to the toxicity and carcinogenicity of β-propiolactone, as well as its multistep process. In 2016, a new selective catalytic process for producing β-propiolactone from ethylene oxide and CO (obtained electrochemically from CO2) on a cobalt catalyst was developed[43, 44]. This technology significantly enhances safety, as β-propiolactone can be used in the form of a harmless polymer poly(3-hydroxypropionate). This polymer can be transported to the AA production site without special precautions, straight for the conversion of the polymer to glacial AA.
In the ethylenecyanohydrin process (1941 – 1945), ethylene oxide is treated with hydrocyanic acid to form ethylenecyanohydrin (Scheme 4). The ethylenecyanohydrin is then dehydrated to acrylonitrile and further hydrolyzed in the presence of sulfuric acid. This process was utilized by several industrial companies, but was discontinued due to issues related to toxic HCN and waste NH4HSO4[1, 45].
In the early 1960s, due to the decreasing price of acrylonitrile, which could be produced more safely and efficiently through the catalytic ammoxidation of propylene, Standard Oil Co. (SOHIO) and Societe Ugine Company developed their own process for the production of AA through the hydrolysis of nitrile (Scheme 5)[46]. The hydrolysis process consists of two stages: first, the hydrolysis of nitrile to acrylamide at 90 °C in the presence of sulfuric acid, and then the methanolysis of the acrylamide to methyl acrylate at 150 °C. This method has been successfully utilized by several companies in Japan and China. However, despite its simplicity and efficiency, there are significant drawbacks to this process. One major issue is the generation of a large amount of ammonium hydrosulfate waste, which is difficult to process. Additionally, the process relies heavily on the cost of propylene, which is the raw material for acrylonitrile. Furthermore, up to 10% of toxic hydrocyanic acid is produced during the synthesis of acrylonitrile. Nevertheless, it is noted that Japan still continues to employ this method for the synthesis of methyl acrylate[1].
One promising trend in AA production is the use of various types of renewable raw materials such as glucose[47], glycerol[48], lactic acid derivatives (lactide derivatives)[49, 50], furfural[51] and others. Despite their environmentally friendly nature, these methods are multi-stage and require further research to achieve economic feasibility and meet other parameters necessary for industrial production.
To date, the primary method for large-scale production of AA is the two-stage oxidation of propylene on heterogeneous catalysts to convert propylene to acrolein and then to AA, making it a highly efficient process (Scheme 6)[1, 45]. Each stage of this process has its own kinetics and optimal conditions (stage 1 – 320 °C, stage 2 – 220 °C) and requires the use of unique polymetallic oxide catalysts including oxides of Bi, Mo, Fe, W, Si, K, V, Cu, Cr, and Al[45]. Typical catalytic compositions are shown in Scheme 6. Despite the complex composition of the catalysts, both reaction steps have high yields (94% and 98%) and selectivity (96% for acrolein). The process uses the hazardous oxidizing agent oxygen and the relatively expensive propylene. The method involves two steps, and the catalysts have a very specific formula. Due to significant differences in the conditions under which each stage is carried out, it has not yet been possible to elaborate an industrial one-step process.
We can also mention the method of synthesizing AA through the direct oxidation of propane using mixed Mo – V – Te – Nb-oxide catalysts. This approach has been studied by several companies, including Mitsubishi Rayon, Rohm & Haas, Toagosei, Arkema, BASF, etc. However, as of now, industrial technology for this process has not been developed[52-56].
The primary advantages of the ‘dream reaction’, which involves the production of AA from ethylene and CO2 (see Scheme 1), are its one-stage process and the availability of reagents. CO2 is a waste product with an emission volume of gigatonnes, and ethylene, one of the most abundant products in petrochemical synthesis, is more competitive than propylene.
Both alkenes, ethylene and propylene, are produced through thermal cracking (steam cracking) of hydrocarbons at high temperature, resulting in a mixture consisting mainly of ethylene, propylene and butylene. The composition and yield of the main products, namely ethylene and propylene, depend on the feedstock used, which includes ethane / propane / naphtha (ligroin)/gasoil (Table 1)[57].
Based on the efficiency of the respective processes, the relative cost of ethylene production from different feedstock sources is as follows: ethane/propane/naphtha (ligroin)/gasoil = 1.0/1.2/1.4/1.5. Therefore, the most cost-effective method is ethane cracking, while propylene production is significantly more expensive due to its low yield. It is important to note that these ratios do not account for the difference in the cost of the feedstock itself or the impact of volatility in the crude oil prices. As of 2024, Brent crude oil prices remain >$80 per barrel. Consequently, in the first quarter of 2024, propane prices in Asian spot markets reached as high as $660 per ton, while ethane prices were around $230 per ton and naphtha prices were as high as $667 per ton. In South America prices for the corresponding raw materials were $439, $143 and $671 per ton (Table 2).
Thus, the synthesis of AA through the carboxylation of ethylene offers significant advantages compared to the current method of oxidizing propylene, which is more costly to produce. In the future ethylene may even be available from such renewable source as bioethanol directing the ‘dream reaction’ onto the path of sustainable technological development. Along with the single-stage production of AA with simultaneous utilization of carbon dioxide, the accessibility of ethylene makes the implementation of this method extremely attractive and relevant especially for industry.
3. Development of AA synthesis
The search for a methodology for ethylene carboxylation has a long history spanning nearly 50 years. The main milestones of this journey are depicted schematically in Figure 2.
The initial stage of development led to the discovery of stable 3- and 5-membered Ni-lactones formed through the interaction of Ni-complexes with CO2, including its insertion onto the C=C bond of coordinated alkenes. The importance and challenge of implementing the β-elimination process in the 5-membered Ni-lactone following its conversion into an acrylate moiety were recognized in the second stage. In the third stage a key transition was made from attempting to obtain AA itself to obtaining sodium acrylate. This stage can be considered the most eventful, with remarkable advancements made possible by accumulating data on the properties of catalytic systems, types of ligands, metals and bases suitable for the efficient synthesis of acrylate derivatives. At the same time parallel efforts were made to elaborate on the transfer of laboratory conditions to industrial technologies.
In the first stage, Aresta with co-workers[58] first synthesized and characterized a 3-membered Ni-lactone with η2-CO-coordination of the CO2 molecule, by performing its metal activation (Scheme 7). In this lactone, the degree of oxidation of Ni is not unambiguous. Based on the character of the complex formation and exchange reactions of neutral ligands — trialkylphosphine on CO2, CO2 on ethylene or hydrogen — one can conclude that Ni in it is in oxidation state (0). At the same time, the deviation from linearity of the coordinated CO2 molecule suggests that it has some properties of СО2–•, as well as nickel has properties of Ni(II), if we consider the formation of Ni – O and Ni – C bonds in intermediates formed during the interconversion of coordinated CO2[59, 60]. In nature, there is a close process of partial reduction of CO2 to CO, proceeding with the participation of [NiFe] – CO-dehydrogenase[61] and being a formal oxidative addition of the C=O bond (in CO2) to nulvalent nickel. A characteristic feature of metallalactones, confirming their carboxylate nature is the chemical shift of the nuclei 13C of the CO2 fragment in NMR spectra, which is in the area of 160 ppm and higher, in contrast to free CO2 with a shift of 124.8 ppm. Interestingly, η2-CO-bound CO2 shows itself as a good O-nucleophile, so it is easily protonated by acids[59].
In 1982, Hoberg and Schaefer[62] synthesized a 5-membered Ni-lactone from Ni(COD)2, norbornene, and CO2 (1 bar), which laid the groundwork for numerous subsequent synthetic studies. Using other alkenes and acetylenes, Hoberg synthesized several Ni-lactones and explored their chemical properties in various stoichiometric transformations such as cycle expansion, acidic cleavage into carboxylic acids, ligand-exchange reactions, etc[63-65]. The synthesis of a 7-membered Ni-lactone from 1,3-diene was achieved by Walther and Dinjus during the same period[66, 67]. However, all attempts to cleave Ni-lactone into acrylic derivatives were unsuccessful until 1986, when Hoberg discovered that Ni-lactone obtained from styrene could undergo β-H-elimination[68], starting already at 85 °C and resulting in the formation of cinnamic acid (70%). By using complexes with DBU-ligands, he successfully carried out β-H-elimination in the seven-membered cycle to produce two isomeric pentenoic acids (79%) (see Scheme 7)[69]. Over the next 20 years there was little progress in finding a solution to the problem of synthesizing AA itself. However, in 2006 Walther with co-authors[70], made a significant breakthrough when they observed the formation of an acrylate κ,κ-O,O-complex (65%) for the first time. This complex was a binickel derivative with a Ni(I) – Ni(I)-bond formed using bis(diphenylphosphino)methane (dppm-ligand) (Scheme 8). The reaction involved the exchange of TMEDA-Ni-lactone for the dppm-ligand at 60 °C. Analysis of the reaction mechanism using deuterated lactone [(TMEDA)Ni(C2D4COO)] revealed that the β-elimination of deuterium (or hydrogen in the conventional lactone) was the rate-determining step. The authors proposed that through the exchange of phosphine ligands along with partial decarboxylation and deethenylation, a tris-phosphine — dppm-complex was formed, which together with the hydride complex produced the binickel product. Despite this discovery, the authors were unable to explain the origin of the intermediate hydride acrylate complex, which hadn’t been obtained previously (see Scheme 8), and did not advance in this study.
It became evident that the 5-membered Ni-lactone, being a highly stable cycle, requires additional stimuli for its transformation into AA. For example, internal stabilization of the C=C bond by the Ph-group, as seen in the cinnamyl derivative synthesized by Hoberg (see Scheme 7) or a decrease in the stability of the cycle itself, as in the 7-membered lactone. In this search for ways to target the transformation of Ni-lactone, Rieger with co-authors in 2010[71] suggested treating Ni-lactone with MeI to break the Ni – O bond. This idea proved successful, but methyl acrylate was only obtained in moderate yields (Scheme 9). It is assumed that the acyclic Ni-derivative undergoes a β-hydride shift more readily to form methyl acrylate, leading to Ni(0), which could then regenerate the Ni-lactone again under the influence of CO2 and ethylene. A study on the synthesis of methyl acrylate from Ni-lactones with TMEDA, 1,2-bis(diphenylphosphino)ethane (dppe), 1,2-bis(diphenylphosphino)propane (dppp), 1,2-bis(diphenylphosphino)butane (dppb) and pyridine, showed a dependence of methylation on the type of ligand[72]. Methyl acrylate was only formed with the first three ligands, with the highest yield achieved with the TMEDA-ligand (for 3 h and with 100 equiv. MeI) being 29% (40% according to IR spectroscopy or 56% according to NMR).
DFT calculations reveal that interaction of MeI with Ni-lactone results in the highest activation energy, leading to the formation of pentacoordinated Ni particles and a tricoordinated oxygen atom in the Ni – O bond in the transition state.
In a subsequent study by Limbach and Hoffmann with coauthors it was demonstrated[73] that Ni-lactone with the bulky 1,2-bis(di-tert-butylphosphino)ethane — dtbpe-ligand is preferentially methylated through the C=O-group, resulting in the opening of the lactone ring as the pathway with the lowest energy (Scheme 10). This methylation pathway was experimentally confirmed. Methylation with methyl triflate was conducted through the carbonyl group, followed by the exchange of the triflate anion with [BAr4F]– (BARF-anion). Treatment of the synthesized cationic complex, with Et3N in CD2Cl2 produced a π-complex of methyl acrylate (15%) within 5 min. Newer data on quantum chemical calculations of the methylation mechanism, the impact of solvents, halogens in the methyl derivative, and other factors are discussed by Liu and co-workers[74].
A new era in the study of Ni-lactones began after Limbach and co-workers[75] developed the catalytic synthesis of sodium acrylate. In 2007, Buntine with co-authors[76] demonstrated that a major challenge in obtaining AA through the ‘dream reaction’ was the unfavorable thermodynamic factors. Both in the gas phase (+57.4 kJ mol–1) and in solution (+42.7 kJ mol–1) the process is endothermic and does not proceed spontaneously (Scheme 11).
Upon synthesis of the methyl ester of AA, the thermodynamics are also unfavorable. Limbach suggested[75], that converting the acid into the salt form could facilitate the reaction. In this case, the Gibbs energy changes its sign (–59 kJ mol–1) and the reaction becomes thermodynamically feasible, with the final product — sodium acrylate — gaining significant energy. Bernskoetter with co-authors[77] studied the influence of the metal cation (Na+) on the energy characteristics of the intermediates in the preparation of acrylate. They showed that the presence of the sodium cation and the formation of salted forms with it reduce the energy of all intermediates (Figure 3). According to Bernskoetter’s DFT calculations, there are four intermediates in addition to g-lactone on the reaction coordinate. These include agostically bound g- and β-H-intermediates, acrylate coordinated to Ni-hydride, and β-lactone with a 4-membered cycle. Under normal conditions, the transformation to Ni-hydride acrylate and β-lactone results in a positive charge on the Ni atom and a negative charge on the carboxyl group with the energies of such intermediates being as high as up to 117.6 kJ mol–1. The interaction of g-lactone with sodium cations (as a trimolecular THF solvate) significantly decreases the relative energy (from 21.6 to 37.1 kJ mol–1) for the high-energy intermediates. Furthermore, the Na-β-lactone is found to be 9.77 kJ mol–1 more stable than the original Na-γ-lactone. XRD data confirm the weakening of the Ni – O bond in the complex with NaBAr4F (the Ni – O bond length increases by 0.057 Å). NMR spectra indicate that this complex shifts into equilibrium with Na-β-lactone when heated to 45 – 78 °C, but its content remains in the range of 25 – 33%, meaning experimentally its energy is higher than that of Na-g-lactone.
In general, the calculated data from Bernskoetter[77] align well with the experimental results from Limbach[75]. Limbach studied the impact of bidentate phosphine ligands (dppm, dppe, dppp, dtbpm, dtbpe and dtbpp) on the formation of Ni-lactone from CO2 (6 bar) and ethylene (2 bar). Among the ligands tested, lactone formation was only observed with dtbpe (35%) and dtbpm (60%). Additionally, the Ni-lactone with the dtbpm-ligand immediately decomposes back into the initial gases upon pressure decrease. In contrast, the lactone with dtbpe remains stable and can be stored in an inert atmosphere for several months without any changes.
However, when ButONa is used, the dtbpe-Ni-lactone easily transforms into an η2-C,C-complex of sodium acrylate in a high yield (Scheme 12). The release of the reaction product, sodium acrylate, is catalyzed by ethylene in the catalytic cycle. The authors successfully conducted an 18-fold recycling of the entire process and achieved TON = 10. The acrylate TON was measured by NMR in D2O solution using an internal standard.
Quantum chemical modeling for systems using strong bases such as ButONa or MeONa as shown by Limbach[75] revealed that the sodium ion coordinates to the carbonyl group of the lactone, activating it. However, for an alkoxylate with a quaternary ammonium cation, this process does not occur. This finding is consistent with the data presented by Bernskoetter[77]. In a DFT study Limbach also demonstrated that the transformation of lactone in the presence of alcoholate (with an alcoholate cluster coordinated through Na) is more likely to occur through the simultaneous abstraction of the α-proton adjacent to the carboxyl group and the formation of a π-complex with sodium acrylate. The authors do not rule out the involvement of the alkoxide anion in the Ni – O bond breakage of the lactone, but note that the process of β-hydride elimination requires high activation energies.
However, the step-by-step procedure of catalyst recycling developed by Limbach, involving pressure relief, changing the type and composition of gases turned out to be so complicated that Vogt and co-workers[78] noted the impracticality of this approach. They proposed using lithium salts as stronger Lewis acids to facilitate all stages of Ni-lactone transformation (Scheme 13). According to DFT calculations, when using a system with a weak base (triethylamine) and lithium iodide, the β-H-elimination process appears to be preferred. The role of the base, according to the authors, likely facilitates the reductive elimination of HI[78]. In this case, lithium ions facilitate the entire process of β-H-elimination by 20 kJ mol–1 better than sodium ions. The authors confirmed their idea experimentally; the transformation of dppe-Ni-lactone into lithium acrylate (73%) with 5 equiv. LiI proceeds without a base, although the addition of 50 equiv. Et3N increases the yield of acrylate up to 95%. The addition of Zn improves the activity of the catalyst but is not essential, while in the absence of LiI the reaction totally fails. Under optimal conditions with dcpp-ligand (1,3-bis(dicyclohexylphosphino)propane) and an ethylene pressure of 25 bar, the TON of the reaction was 14 – 21. The authors also noted the formation of by-products that reduced the catalysis efficiency.
Limbach with co-workers[79] also updated the initial synthesis conditions, which involved replacing the base and ligand (Scheme 14). The need to replace the base was explained by the fact that alcoholates and strong basic amines (like DBU) are irreversibly neutralized by CO2, while phenolates react reversibly with CO2 due to their lower nucleophilicity. This behavior of phenolates was already known from the Kolbe – Schmitt carboxylation reaction of phenolates. Using sodium 3-fluorophenolate, phosphine ligands were screened, and although the BenzP*-ligand was not the most active at 80 °C (DuanPhos, TangPhos ligands were more efficient), it became the most productive at higher temperatures. Optimization of all parameters led to relatively high TONs of sodium acrylate. The most efficient were 3- and 2-fluoro-substituted sodium phenolates, with TON reaching 35 at 100 °C, although further temperature increases had a negative impact. Increasing the amount of base to 100 equiv. had little significance, while adding the reducing agent Zn and increasing pressure produced a stronger effect — 300 equiv. of base and 100 equiv. of zinc with a doubled gas pressure resulted in the highest value of TON = 107. The catalytic process showed high efficiency not only in the reaction with ethylene, but also with other alkenes (see Scheme 14). Significantly high values of TON = 75 – 116 were obtained with vinylic derivatives almost regardless of the electronic character of the substituents with the C=C bond of the alkene.
Bernskoetter and co-workers[80], noting the presence of chiral centers in the BenzP*-ligand as an unnecessary and complicating factor, proposed the use of a symmetric achiral analogue — PriBenzP-ligand (Scheme 15). However, the synthesized PriBenzP showed worse results — TON = 45 compared to 82 with BenzP*. The LiI additive revealed an inhibitory effect (TON = 14 and 30), while Zn additive was favorable in both cases (TON = 84 and 109). The most interesting finding was the use of the less basic sodium 2-chlorophenolate, which was ineffective with PriBenzP (TON = 30), but surprisingly increased the catalyst activity (TON = 135) in the presence of BenzP*. Furthermore, with NaI additive the TON value was significantly increased to previously unattainable levels (TON = 404). Actually, the role of each additive is not fully elucidated, as the authors point out, due to ‘there exist multiple interactions between the Zn reductant, Lewis acidic salts, phenoxide bases, and nickel species employed in these catalytic systems’[80].
Seeking more information on the structure-activity relationship (SAR) of previously synthesized BenzP-type ligands, Bernskoetter with co-workers[81] performed a joint screening of ligands and phenolate bases. However, despite their efforts, they were unable to propose an approach to selecting ligands and bases that would allow for the directed design of catalytic systems. For diphosphine Ni complexes, they only proposed a model of coordination sphere quadrants suggesting that the optimal characteristics are found in a BenzP-ligand with alternating hindered and freer quadrants. In this study, the researchers obtained data on the TON of the catalyst dependence on the electronic and steric characteristics of the phenolate base (Scheme 16). A comparison of the properties revealed the need for a balance of factors: good basicity to facilitate proton cleavage in the Ni-lactone or intermediate particles, and a certain steric environment to maintain access to the Ni-complex while limiting the stability of the carbonate formed during the reaction from sodium phenolate. Experimental data in Scheme 16 illustrate the accumulation of acrylate (dashed line) with sodium 3-fluorophenolate, as well as carbonate accumulation and phenolate consumption. It is evident that after just 10 hours, the reaction is nearly halted, though the addition of a new portion of phenolate (not shown in Scheme 16) reactivates the catalysis.
Previously, Schaub and co-workers[82] conducted a study on the decomposition temperature of carbonates of various bases using the TGA method (Scheme 17). In their study typical phenolate carbonates, that are active in the synthesis of sodium acrylate, decomposed into CO2 and alcoholate at moderate temperatures ranging from 50 to 70 °C. These temperatures were lower than those required for the catalytic reaction. On the other hand, inactive bases like sodium methylate and sodium ethylate, produced carbonates that were too stable to decompose even at temperatures as high as 330 °C.
To determine if the thermal stability of carbonates changes in real conditions under CO2 pressure and in the presence of a solvent, the authors conducted tests on the decomposition of sodium tert-butyl carbonate in an autoclave. The decomposition process was monitored using an integrated IR sensor. The results indicated that the decomposition temperatures were almost identical to those measured under standard conditions. These findings provide insight into why hindered phenolates (see Scheme 16) are more effective as bases.
One reason for the limited reactivity of Ni-catalysts is their oxidation and disproportionation. Therefore, Zn powder is often added to the reaction as a reducing agent. While all authors suggest that Zn enables the reduction of Ni2+ complexes to Ni0, its participation in the catalytic cycle or mechanisms of deactivation are not clearly indicated.
Iwasawa and co-workers[83] set a goal to enhance the stability of Ni-complexes in the synthesis of acrylates. They selected carbene-phosphine-type ligands (NHC-P) because, thanks to the NHC-fragment, they also have a higher donor ability (Scheme 18).
Complexes 1a – d were prepared from imidazolium salts by sequential treatment with ButOK and then Ni(COD)2 in THF. The synthesis of Ni-lactone from ethylene and CO2 with 1a, proceeds within 30 min, whereas the analogous process with dcpe-ligand requires several days. Due to its asymmetric structure, Ni-lactone is obtained as a mixture of spatial isomers. Measurement of the oxidizing potential of 1a (–1.26 V), showed that its reducing ability is significantly higher than that of [Ni(dcpe)(cod)] (–0.95 V). Test experiments of β-H-elimination in lactone with ButOK and ligand exchange of potassium acrylate for ethylene showed good results. Screening of catalysts and conditions for acrylate synthesis revealed a new efficient base for use with the above complexes — sodium mesitolate (MesONa). Apparently, due to the need for a high temperature of 145 °C (lower temperature reduces the yield) to achieve acceptable activity, other phenolates are of little use as they undergo carboxylation by the Kolbe – Schmitt reaction. The addition of sodium acetate together with complex 1a significantly increases the TON value to 94 versus 58 without addition. The maximum efficiency was shown by catalyst 1d (TON = 140), with a decrease in catalyst loading leading to an increase in the TON value to 450, an unprecedented value, thus showing efficiency and adaptability to the conditions for the synthesis of NHC,P-ligands. Interestingly, catalysts 1b,c of close structure were completely inefficient.
Hong and co-workers[84] continued the study of NHC-ligands and synthesized a series of stable NHC,N-ligands 2a – f based on imidazo[1,5-a]pyridine (Scheme 19).
Despite the different substituents in the pyridine and imidazole moieties, the efficiency of such complexes in the synthesis of AA salts remained low at the investigated temperature (TON = 0.34 – 8.45) and did not exceed the activity of standard nickel diphosphine complexes (TON = 9 – 14) tested for comparison.
When applying photoactivation to the developed NHC,P systems, Iwasawa and co-workers[85] unexpectedly obtained a salt of methylmalonic acid instead of AA (Scheme 20).
Earlier in 1991 Hoberg and co-workers demonstrated[86] that a stoichiometric reaction is feasible with Ni-lactone, albeit requiring the presence of BeCl2 (10 bar CO2, 70 °C, THF/Py, 1 : 1) through the formation of a four-membered lactone, while the yield of methylmalonic acid is 50%. In a subsequent study, Iwasawa conducted[85] a photocatalytic synthesis using a 1 bar CO2/ethylene (1 : 1) mixture in DMA solution with 20 mol% Ir(dtbpy)(ppy)2 PF6 and irradiated with 395 nm LED lamps. The optimal conditions included the use of 2 lamps, Cs2CO3 additive (200 equiv.) and the reducing amine (or ‘sacrificial’ amine) DIPEA (100 equiv.). Under these conditions, the NHC,P-complexes exhibited the TON values as follows: 3a — 8.1, 3b — 8.2, 3c — 9.4 and 3d — 8.5, showing close values. The proposed mechanism of this reaction involves the photoinduced insertion of CO2 into the 4-membered Ni-lactone with an alpha-methyl group formed through isomerization, resulting in a malonate Ni(II) derivative. It is worth noting that in Iwasawa’s[85] work, the NHC,N-ligand was one of the least active in catalysis, comparable in activity to the diphosphine dcpe-ligand.
Along with the target coupling reaction and the productive cycle of the Ni-catalyst, there are several side processes associated with the removal of Ni-complexes from the catalytic cycle of acrylate formation. These processes have been analyzed in Limbach’s work (Scheme 21)[23]. The main products associated with the occurrence of side processes and reduced catalyst activity in the target reaction include: 1) Ni0 bis-phosphine complexes; 2) a 3-membered lactone as an intermediate for the competitive coordination of CO2 with ethylene and Ni via η2-type coordination followed by oxidative transformation to nickel carbonate or precipitation of metallic nickel; 3) a 7-membered lactone formed by sequential double introduction of ethylene; 4) a 4-membered lactone obtained by isomerization of a 5-membered lactone, which can form a malonate complex upon introduction of a second CO2 molecule. Oxidation of phosphine by coordinated CO2 is also a side process[60].
Since Ni-based catalysts do not achieve high TON values and require large excesses of base, reducing agent or other additives to increase stability and achieve meaningful activity in the catalytic cycle, the interest in using other metals is of both fundamental and practical importance. Indeed, the carboxylation reaction of ethylene to form metallalactone or acrylate can proceed in the presence of many other metals[87], such as Ti[88], Zr[89], V[90], Mo and W[91-93], Fe[94-96], Ru[97], Rh[98, 99], Pd[100], Co[101] and Al[102]. However, the successful realization of the catalytic reaction is only possible in some systems.
One of the first metals used for catalytic carboxylation of alkenes along with nickel was palladium. Inoue (1976)[103] and Musco (1978)[104] observed the formation of carboxylated telomers from 1,3-butadiene and CO2 in the presence of phosphine complexes of Pd, including 5- and 6-membered unsaturated lactones.
Limbach and co-workers[100] applied Pd-catalysts in the synthesis of acrylate (Scheme 22). They were able to obtain a Pd-lactone for the first time, which was formed as a mixture (1 : 1) with an acrylate complex through the lactonization of η2-coordinated AA. The pure lactone was then isolated through crystallization. Various Pd complexes were tested for the catalytic synthesis, with (COD)PdCl2 and (η5-Cp)Pd(η3-allyl) showing greater activity. The latter complex did not require a reducing agent (Zn). Synthesis conditions for the acrylate were screened using a commercially available (COD)PdCl2. The maximum TON = 29 was achieved when the catalyst loading was reduced by half (0.5 mol.%) from standard conditions (1.0 mol.%), with TON values of 24 (145 °C) and 27 (120 °C). In addition to ethylene, 1,3-butadiene and 1,3-pentadiene readily enter the carboxylation reaction with the catalyst loading of 0.33 and 1.0 mol.% and TON values of 24 and 50, respectively.
In the same year, Schaub and co-workers[105] presented an extensive study dedicated to improving catalytic synthesis conditions and increasing TON values on both Pd and Ni catalysts. This work also aimed to explore catalyst recycling (Table 3).
Initial screening of phenolate bases showed that the 2-methyl- and 2,6-dimethyl derivatives allowed relatively high TONs to be achieved with Pd- (TON = 38) and Ni-catalysts (TON = 69) in the presence of a dcpe-ligand, but a temperature of 145 °C was required. The lipophilic sodium 2,6-dimethyl phenolate was also considered a better base for the continuous process, where the sodium acrylate should be separated by aqueous treatment in a two-phase system with phenolate regeneration through an organic solvent. The authors were able to reduce the amount of Zn-reductant to 5 equiv. and show that even in its absence the catalysts continue to work, but the reduction in TON could not be avoided. However, as Schaub points out, the need to introduce a reducing agent adds complexity and cost to the process. These tests revealed that the nulvalent palladium complex Pd(PPh3)4 without the addition of Zn has acceptable productivity characteristics (TON = 28). Furthermore, a suitable solvent such as anisole was identified to ensure compatibility with the catalytic system and immiscibility with water during the acrylate extraction and catalyst regeneration step. Moreover, only in the case of Pd(PPh3)4, almost no drop in catalyst productivity was observed when switching from fresh dry anisole to wet solvent in the recycling step. The phenolic base structure was also optimized to avoid phenol loss during the acrylate separation step. The best TON = 50 was obtained with 2,6-diBut-4-MePhONa, whose conversion was almost quantitative (99%) and its loss resulting recycling was only 0.6%.
A crucial step in the recycling procedure of the catalytic process was washing the product and excess base with water to remove the catalyst and ligand, which remained in the organic layer. Table 4 provides a summary of the TON values for the first and second catalyst cycles. Despite conducting all manipulations of the second cycle in an inert atmosphere, the catalyst’s activity decreased significantly.
The addition of a reducing agent was necessary to maintain acceptable activity in the second cycle, indicating oxidation of the complexes during the product separation manipulations. Furthermore, the TON values still remained several times lower than in the first cycle. Through extensive screening of catalytic synthesis conditions, Schaub was able to develop a more efficient system for the synthesis of sodium acrylate, though it was still far from practical use.
Schaub further demonstrated[82] that an appreciable efficiency (TON = 50) can be achieved with Pd(PPh3)4 using ButONa (50 equiv.), while the potassium and lithium salts yield lower TON values, showing 41 and 33, respectively. tert-Butylate has a significantly lower molecular weight compared to substituted phenolates, allowing for a higher concentration of base in the reaction medium of 0.66 M (20 mmol), resulting in a TON = 88. By reducing the catalyst loading (to 1.0 μmol) the maximum TON value of 100 was achieved in 65 h. It is important to note that the simultaneous catalyst deactivation process hinders the TON value from increasing proportionally to the decrease in catalyst loading. The carboxylation of various alkenes was screened under optimized conditions (Scheme 23). Notably, 1,3-butadiene showed exceptional reactivity, completing the reaction within 3 h at 100 °C compared to standard conditions of 20 h at 145 °C, surpassing previous reactivity achieved with Ni-catalyst. The carboxylation of styrene followed a similar pattern to Ni-systems. Propylene and hexene-1 produced a mixture of linear and branched products (l/b), with propylene carboxylation demonstrating high efficiency for the first time. The crotonate/methacrylate ratio for propylene was 1.4, while the ratio of the corresponding products for hexene-1 was 3.3. Cyclic acrylates were obtained with low TON values (see Scheme 23).
Assuming that the Pd-acrylate complex can agglomerate in low-polarity solvents like anisole, Schaub with co-authors[106] used amide solvents (Scheme 24, DBF, N,N-dibutylformamide; NMP, N-Me-pyrrolidone; CHP, N-cyclohexylpyrrolidone), which are much more compatible with the developed catalytic system. These solvents not only stabilize the catalytically active Pd species, but also dissolve CO2 better. In contrast to anisole, increasing the CO2 pressure from 20 to 40 bar in amide solvents significantly increases activity, and the combination with ButONa makes the reaction even more efficient. The TON value reaches 152, and when the catalyst loading is reduced by a factor of 10 (0.01 mmol) it reaches 514 (for 5 h TON = 307, TOF = 61 h–1). For anisole, the TOF value for 15 h was only 5 h–1. These activity values were unattainable earlier and are promising for the development of an industrial synthesis scheme. At the same time the reuse of the catalytic system even increases its activity (Table 5). Furthermore, the success of the developed system is evident in the 100% conversion rate of the base, along with the option to utilize the more technologically advanced and cost-effective PriONa, albeit with lower efficiency in the initial stage.
The authors have proposed an optimized process flow diagram for the continuous synthesis of sodium acrylate. This diagram takes into account the separation of the reaction product by water, as well as the regeneration of alcoholate and catalyst solution in an amide solvent. Additionally, provision is made for the removal of traces of water from the solvent under mild vacuum conditions (Figure 4).
In this way the use of amide solvents improved both the catalytic activity and facilitated the recycling of the entire reaction mass. The achieved TON value > 500 combined with the use of inexpensive and readily available bases provides a solid foundation for further technological advancements in the continuous synthesis of sodium acrylate. The technological aspects of the process development for the synthesis of acrylic acids salts are outlined in a series of patents[107-110].
It is worth noting that Chevron chemists also attempted to develop a technological process using nickel complexes. In their 2018 patent[111] they utilized a salt form of ion-exchange polystyrene resin with sulfonate, phosphonate, sulfinate, thiosulfonate and thiosulfinate groups as a base, including commercial resins such as Amberlite and Amberlyst. This modification simplifies the separation of the solid pure reaction product from the catalyst. However, the acrylate yield reported in the patent when using the sodium salt of Amberlite resin was only 6.7%. It is impossible to assess the effectiveness of using other resins based on the information provided in the patent.
In the next patent by these authors[112] the following modified metal oxides were developed: chemically modified solid oxide (CMSO) and metal treated chemically modified solid oxide (MT-CMSO), which also acted as a heterogeneous base. The patent presents data for several modified oxides, among which the best acrylate yields were shown by aluminum oxide treated with sodium tert-butylate, as well as Amberlyst 36 resin treated with sodium tert-butylate. In the presence of Ni(COD)2/dcpe catalytic system in toluene (CO2 / C2H4, 1 : 1, 20 bar, 100 °C, 6 h) and modified aluminum oxide, yields of more than 1200% as per nickel were achieved (Table 6). It is difficult to assess how convenient this reaction methodology is with respect to the use of ButONa solution or suspension, but its efficiency was significantly lower (maximum TON = 12.4).
In the 2023 patent[113] the techniques for using metal oxides (CMSO, MT-CMSO) and ion exchange resins were improved and a nickel-containing catalyst deposited on such a carrier was proposed. The deposition on the oxide was carried out from THF in situ using Ni-lactone derived from Ni(COD)2/dcpe in CO2/C2H4. These systems can catalyze the synthesis of acrylate not only in the presence of solvent, but also without a solvent, i.e. in a gas-phase heterogeneous system to achieve TON values up to 148 at 120 °C. A regeneration procedure was also proposed for the Ni-catalyst when its activity decreases. The main disadvantage of the process is the necessity to isolate the acrylic acid salt by solvent washing.
Interesting results were presented in the work by Vavasori with co-authors[114], who showed that traditionally inactive monodentate phosphines (PPh3, PBut3) in Ni(0)-catalysis, as well as chelate diphosphines with a small ‘bite angle’ (e.g., dtbpm and dppm)[79], work effectively as simple Ni(II) and Pd(II) complexes ([NiCl2(PPh3)2], [PdCl2(PPh3)2 ]) in the synthesis of sodium acrylate. Under the specified conditions (Na-phenolate/[M] = 500/1 mol/mol; C2H4 (25 bar); CO2 (25 bar); THF (25 mL); 90 °C; 20 h), good TON values on Ni(II) and Pd(II) (0.038 mol) of 280 and 222, respectively, are achieved, which decrease with decreasing catalyst loading. Bidentate ligands (dmmp, dppe, dppp, dppb, Xantphos) were tested, revealing a linear increase in catalyst TON with increasing phosphine ‘bite angle’. It is shown that the TON value significantly increases with temperature with the dppp ligand showing an increase from 33 (at 30 °C) to 290 (at 130 °C) for the complex [NiCl2(dppp)], while the TON for [PdCl2(dppp)] increased from 3 (at 30 °C) to 111 (at 130 °C). The TON dependence on the type of base cation (Na+ or K+) and its concentration is also presented in this work. Curious results were obtained from the solvent screening of [NiCl2(dppp)], where the most effective were polar aprotic solvents — acetone (TON = 273) and DMSO (TON = 290), which had not been previously used in the catalytic synthesis of acrylate. Relatively high TONs were also achieved in alcoholic solvents with the best results in 1- and 2-propanols (TON = 261 and 244, respectively). However, despite the demonstrated results, the authors did not present a proposed mechanism of the process to explain how the catalytic system functions through the cationic forms of metals (Ni(II) and Pd(II)).
In addition to palladium and nickel compounds, systems based on rhodium and ruthenium complexes are active in the catalytic carboxylation of ethylene. In 1993 Aresta and Quaranta[99] observed the precipitation of solid Rh-lactone as a result of slow carboxylation (1 bar CO2, THF, 25 °C, 9 days) of the ethylene complex (bpy)Rh(I)Cl(C2H4). Confirmation of the lactone structure was made based of NMR and IR spectroscopy data. In 2022, Nakao and co-workers[98] performed the catalytic synthesis of acrylates using pincer complexes of Rh with aminoguanidine ligands (Scheme 25). Hydride Rh(III)-complex 4a, ethylene Rh(I)-complex 4b, maleimide Rh(I)-complex 4c, and the pincer phosphine complex 4d were tested, with the pincer phosphine complex 4d used for comparison. Complexes 4b,c are derivatives of complex 4a and are obtained by treatment of the latter with ButOK in benzene, followed by complexation with ethylene or N-methylmaleimide. One of the key stages of synthesis, the coupling of ethylene and CO2 to form Rh-lactone (78%), was confirmed by its synthesis from 4a. However, the efficiency of this system remains low with a maximum TON of 7.7 at 160 °C. The transition from low-polarity solvents such as toluene and anisole to dimethylacetamide does not result in increased efficiency.
Iwasawa and co-workers[97] obtained very interesting results on Ru(0) derivatives. First, the authors synthesized the known stabilized by tetradentate phosphine ligand ethylene complex of Ru(0) 5[115, 116], and then investigated its ability to form Ru-lactone 6 (Scheme 26).
The yield of 6 in direct coupling of the ethylene complex 5 with CO2 is 71% by NMR and 55% in the isolated form. In this process all transformations for ruthenium are of equilibrium character, allowing for a complete catalytic cycle from any intermediates. Particularly, the exchange of the acrylate fragment in 8 to ethylene (route A) in the presence of potassium ethylate proceeds with an efficiency of 96%. Meanwhile, the crucial key step of β-elimination in Ru-lactone (route B) to form a hydride complex of acrylate 8 (24%) proceeds simply upon heating to 100 °C. The reverse process of recyclization to lactone 6 proceeds at 60 °C in quantitative yield. Although the catalytic efficiency was rather low (maximum TON = 6) compared to nickel and palladium systems, this was the first example of catalytic synthesis of acrylate from ethylene and CO2 using a ruthenium catalyst (Scheme 27).
Due to the ease of transforming Ru-lactone into acrylate through simple thermal rearrangement without the need for any additives, this system shows promise for further development. Therefore, Iwasawa with co-authors[117] continued their research to develop new more efficient catalysts. They synthesized a series of tetradentate phosphine ligands L1 – 4 with varying donor abilities and framework rigidities (Scheme 28).
The preparation of Ru complexes based on L1-4 ligands was carried out in two steps. First, the Ru1-4-OAc hydride-acetate complexes were prepared in good yield, and then ethylene complexes of Ru1-4 were synthesized by treatment with ButOK in an ethylene atmosphere. Based on the NMR chemical shifts of carbon atoms of coordinated ethylene Ru1 (18.6 ppm) > Ru2 (22.1 ppm) > Ru3 (34.8 ppm) > Ru4 (43.1 ppm), the donor ability of phosphine ligands was determined to be in the following order L1 > L2 > L3 > L4. The more donor complexes of ethylene are more rapidly transformed into Ru-lactone (e.g., Ru3 for 15 h and Ru1 for 1 h at 60 °C, whereas Ru4 does not react at all) as well as into an acrylate complex (in CO2/ethylene mixture) of type 4 (see Scheme 26) and then successively enter into rapid exchange with ethylene in the presence of ButOK, regenerating the initial Ru1 complex.
As a result of studying the effect of different strengths of bases on the rate of transformation of Ru-lactone into the Ru3 ethylene complex, it was concluded that there are two pathways for this process (Scheme 29).
According to the authors, in the case of a strong base, pathway 2 is realized with initial proton abstraction from the lactone. In the case of a weak base two pathways can be realized depending on the amount of base present. Testing of Ru1-4-OAc complexes in an actual catalytic process with ButOK revealed that the most active derivatives of ligands L1 and L2 only produced substoichiometric amounts of acrylate. However, the least active Ru4-OAc complex was catalytically active in the lactone formation process (TON = 7.9). Additionally, transitioning to the weaker bases CsOMes and Cs2CO3 slightly increased the yield of acrylate. In the latter case, the Ru4 ethylene complex exhibited the highest TON = 15 with a 1000-fold excess of the weak base and a 4-fold increase in Ru4 loading. Despite this excess, the use of stable cesium carbonate is very convenient for practical applications and demonstrates the characteristic pathway 1 for ruthenium.
At the current stage of research on Ru-catalytic systems, there is insufficient knowledge to understand the ways of catalyst deactivation and how to increase their catalytic efficiency. However, the unique properties of Ru-catalysts that allow for the conversion of the lactone ring into an acrylate fragment under moderate heating conditions make Ru-systems promising for future improvements. It is possible, that they will undergo the same rapid growth of interest and application as we have seen with Ru-catalysts in Grubbs metathesis, which are utilized on both laboratory and industrial scales.
4. Conclusion
This review was written under the influence of the discovery that the reaction of ethylene with CO2 to form the AA salt is quite attainable if suitable conditions (catalysts, additives, base or Lewis acid, solvent, temperature and pressure) are used. It is crucial to note that, unlike the synthesis of AA itself, synthesis of acrylate is exothermic and thermodynamically allowed. However, overcoming thermodynamics does not guarantee acceptable kinetics, as the TON values are still relatively low. The mechanism of this reaction, particularly the decay of the metallacycle and the β-elimination of hydrogen, is not fully understood, as it can involve both β-hydride and β-proton abstraction. The fact that the reaction can be catalyzed by LiI in the absence of a base and can also achieve high (according to available numbers) TOF values with strong bases like ButONa, complicates drawing a definitive conclusion. Nevertheless, it can be affirmed that the catalytic coupling of ethylene and CO2 (direct carboxylation) to form sodium acrylate is a viable synthetic method, that has evolved from a theoretical concept, a ‘dream reaction’, to a technologically advanced process. Initial studies on Ni catalysts show promise but suffer from low stability, hindering catalyst recycling and industrial application. Utilization of more stable mixed nickel phosphine-carbene complexes could enhance the industrial potential of Ni systems. Additionally, simple and stable catalytic systems based on [Pd(PPh3)4] have been identified. Optimization their conditions of use has led to maximum efficiency in sodium acrylate preparation (TON > 500), catalyst recycling without loss of efficiency and full utilization of cost-effective bases like sodium isopropylate or sodium tert-butylate, derived directly from sodium hydroxide and alcohols. Analysis of scientific findings and patent data reveals industrial interest in this process, aiming to develop a competitive alternative to propylene oxidation for AA production. However collaborative efforts are needed to realize this final step.
5. List of abbreviations
AA — acrylic acid;
BARF — tetrakis[3,5-bis(trifluoromethyl)phenyl]borate;
BenzP* — 1,2-bis(tert-butylmethylphosphino)benzene;
CHP — N-cyclohexylpyrrolidone;
CMSO — chemically modified solid oxide;
COD — 1,5-cyclooctadiene;
DBF — N,N-dibutylformamide;
DBU — 1,8-diazabicyclo[5.4.0]undec-7-ene;
DCM — dichloromethane;
Dcpe — 1,2-bis(dicyclohexylphosphino)ethane;
Dcpp — 1,3-bis(dicyclohexylphosphino)propane;
DIPEA — diisopropyl ethylamine;
DFT — density functional theory;
DMA — N,N-dimethylacetamide;
Dmmp — dimethyl methyl phosphonate;
Dppe — 1,2-bis(diphenylphosphino)ethane;
Dppm — bis(diphenylphosphino)methane;
Dppp — 1,3-bis(diphenylphosphino)propane;
Dppb — 1,4-bis(diphenylphosphino)butane;
Dtbpe — 1,2-bis(di-tert-butylphosphino)ethane;
Dtbpm — bis(di-tert-butylphosphino)methane;
Dtbpp — 1,3-bis(di-tert-butylphosphino)propane;
DuanPhos — (1R)-2-tert-butyl-1-[(1R)-2-tert-butyl-1,3-dihydroisophosphinoindol-1-yl]-1,3-dihydroisophosphinindole;
IR — infrared;
Ir(dtbpy)(ppy)2 PF6 — 4,4′-bis(1,1-dimethylethyl)-2,2′-bipyridin-N1,N1′]bis[2-(2-pyridinyl-N)phenyl-C]iridium(III) hexafluorophosphate;
LED — light emission diode;
MT-CMSO — metal treated chemically modified solid oxide;
NHC — N-heterocyclic carbine;
NMP — N-Me-pyrrolidone;
PriBenzP — 1,2-bis(di-iso-propylphosphino)benzene;
SAR — structure-activity relationship;
TangPhos — (1S,2R)-1-tert-butyl-2-[(1S,2R)-1-tert-butylphospholan-2-yl]phospholane;
TMEDA — N,N,N,N',N'-tetramethylethylenediamine;
TOF — turnover frequency;
TON — turnover number;
UV — ultraviolet;
Xantphos — (9,9-dimethyl-9H-xanthene-4,5-diyl)bis(diphenylphosphane).
Acknowledgements
The article was prepared with the financial support of the Ministry of Science and Higher Education of the Russian Federation (agreement No. 075-15-2024-547 dated 24.04.2024).
References
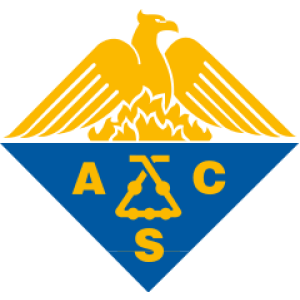
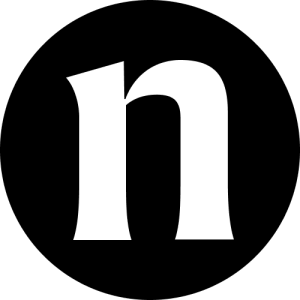
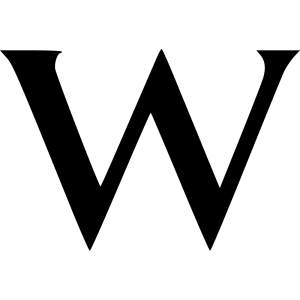
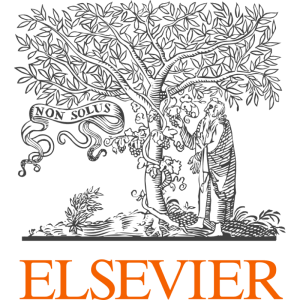
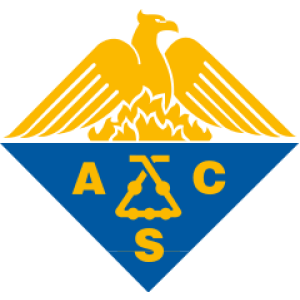
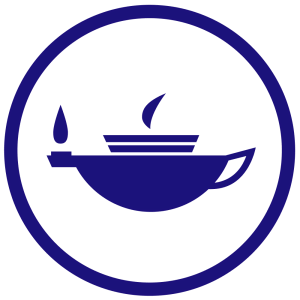
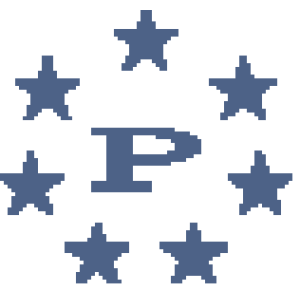
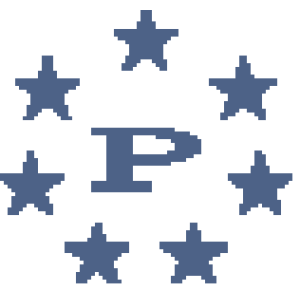
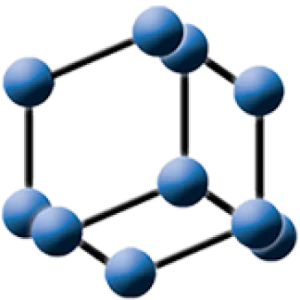
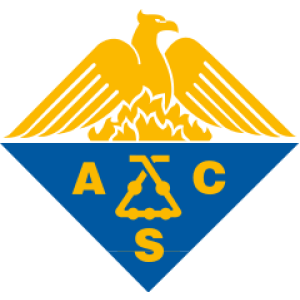
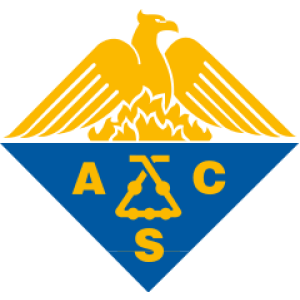
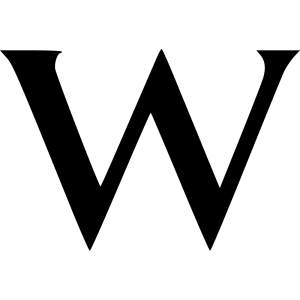
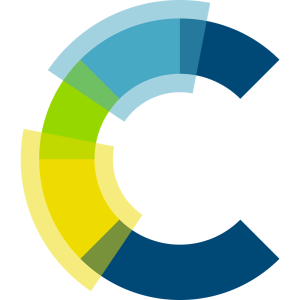
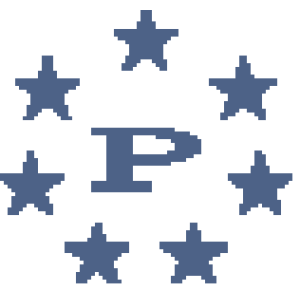
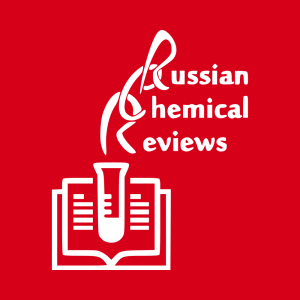
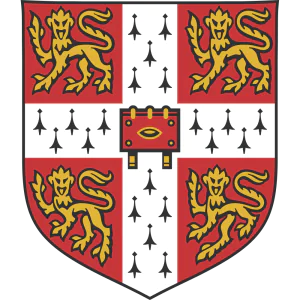
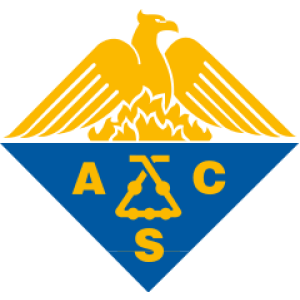
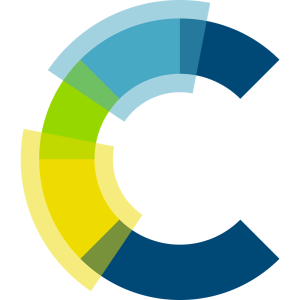
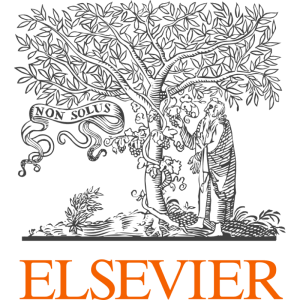
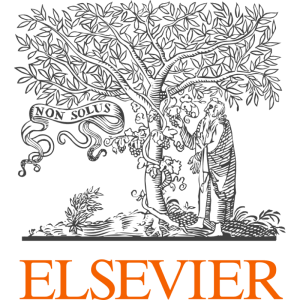
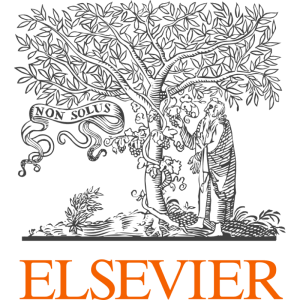
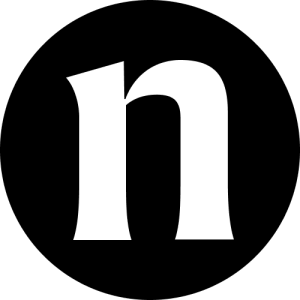
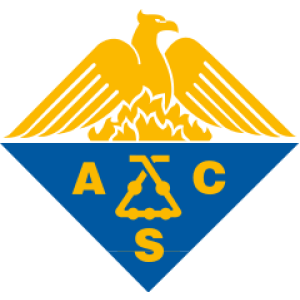
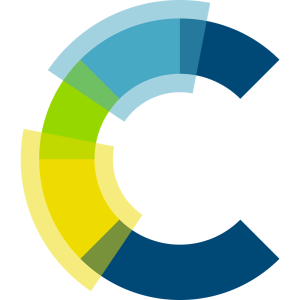
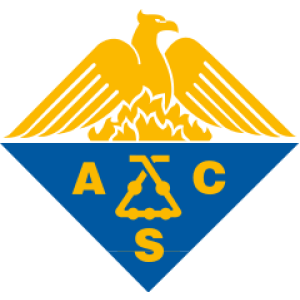
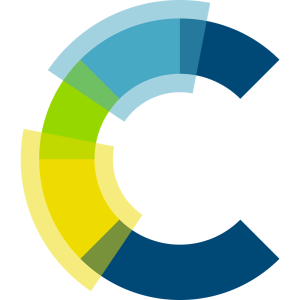
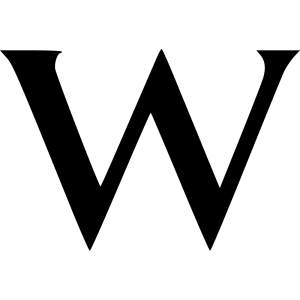
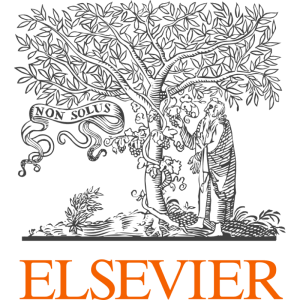
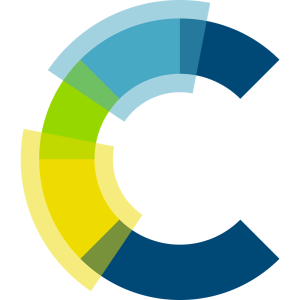
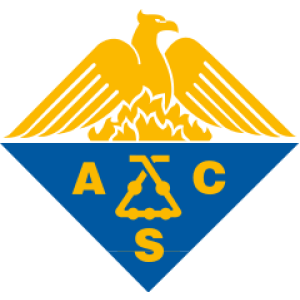
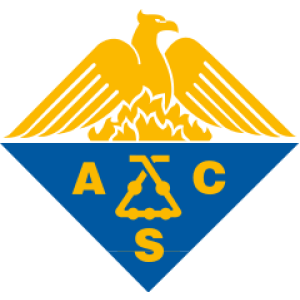
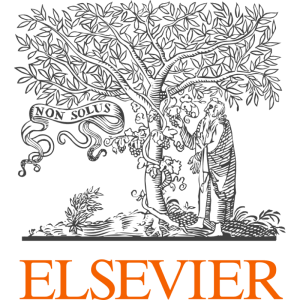
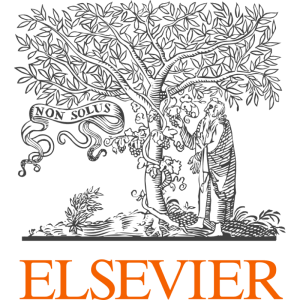
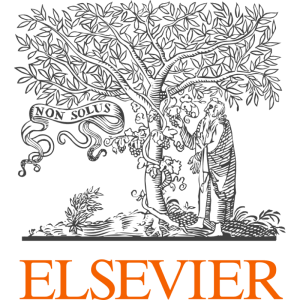
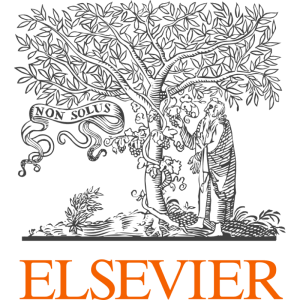
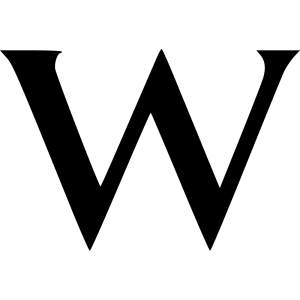
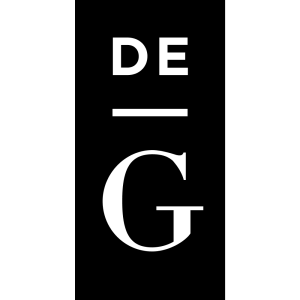
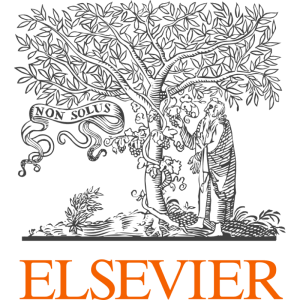
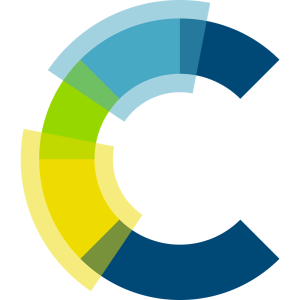
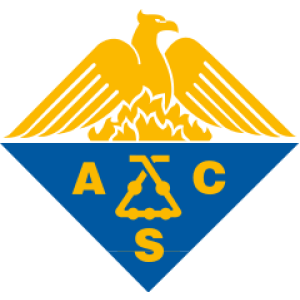
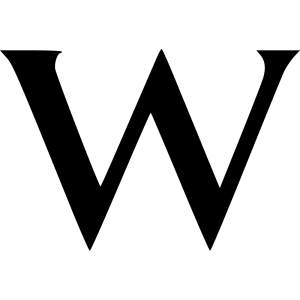
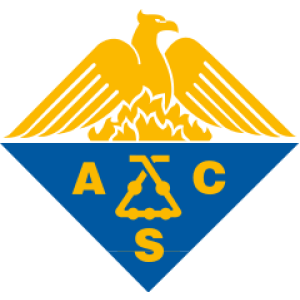
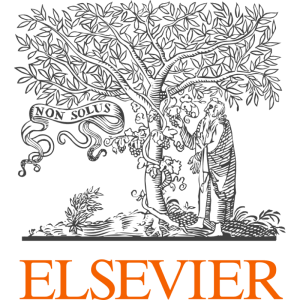
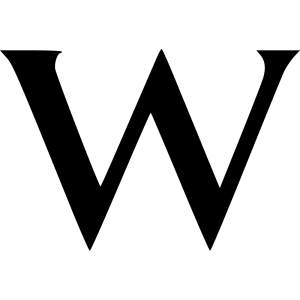
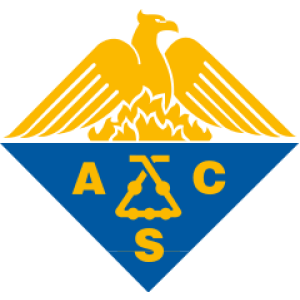
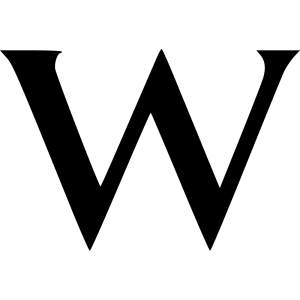
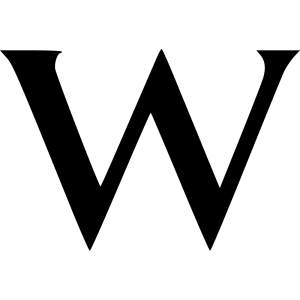
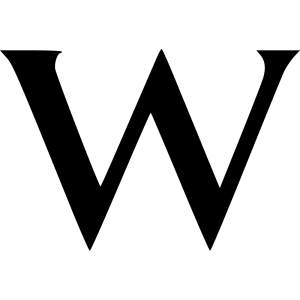
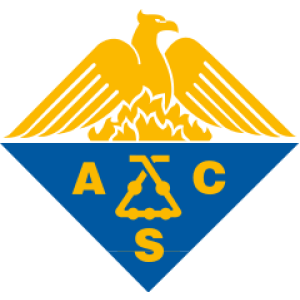
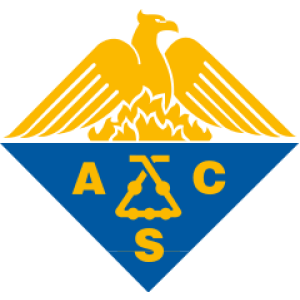
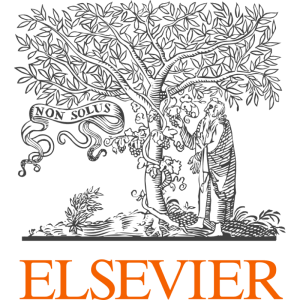
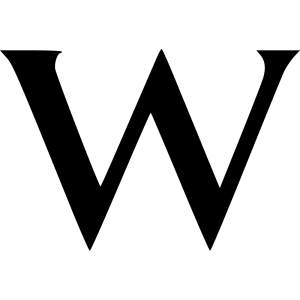
![Pyridine-Chelated Imidazo[1,5-a]Pyridine N-Heterocyclic Carbene Nickel(II) Complexes for Acrylate Synthesis from Ethylene and CO2](/storage/images/resized/MjH1ITP7lMYGxeqUZfkt2BnVLgjkk413jwBV97XX_small_thumb.webp)
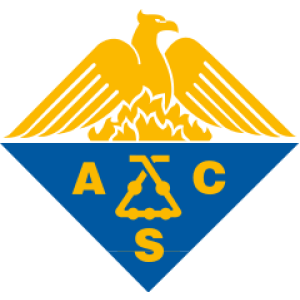
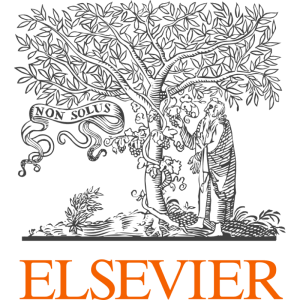
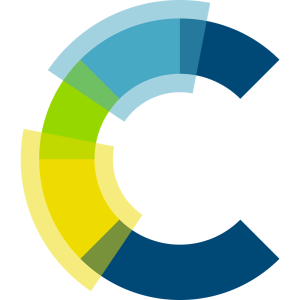
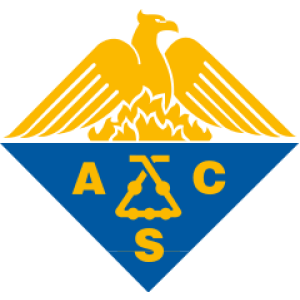
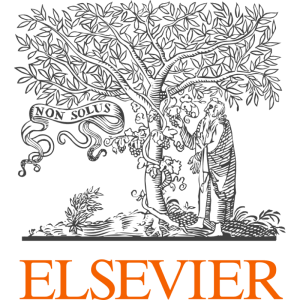
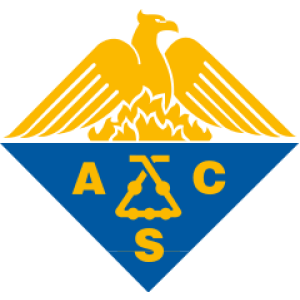
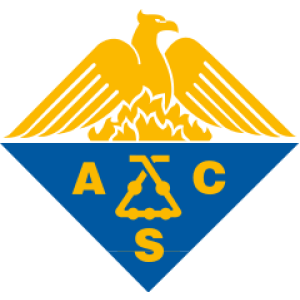
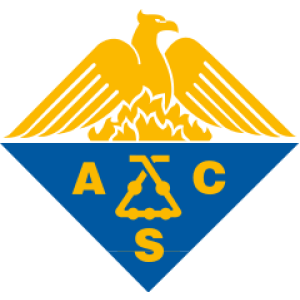
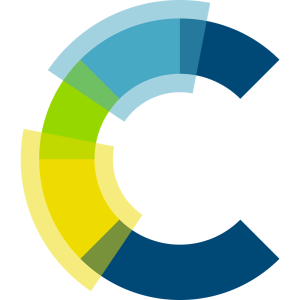
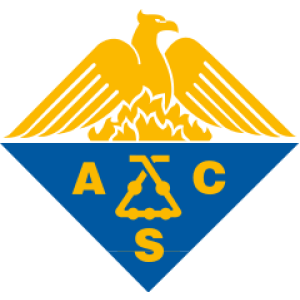
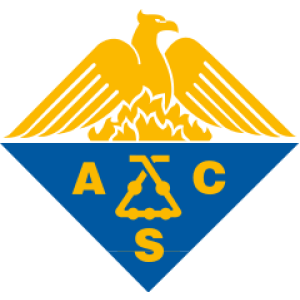
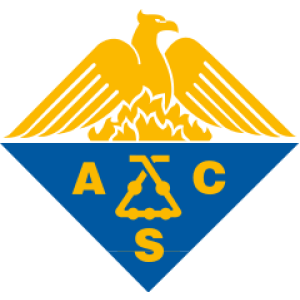
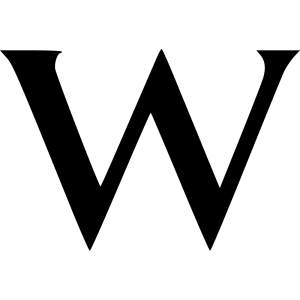
![Synthesis, characterization and reactivity of [Rh(bpy)(C2H4)Cl]. A study on the reaction with C1 molecules (CH2O, CO2) and NaBPh4](/storage/images/resized/GDnYOu1UpMMfMMRV6Aqle4H0YLLsraeD9IP9qScG_small_thumb.webp)
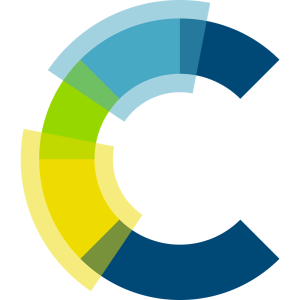
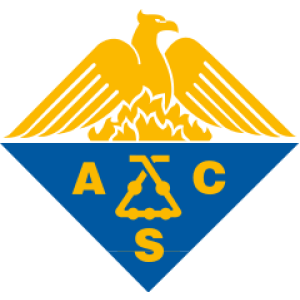
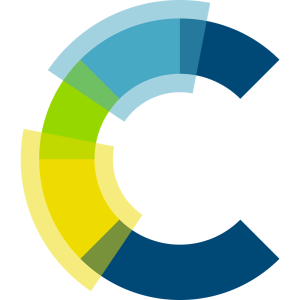
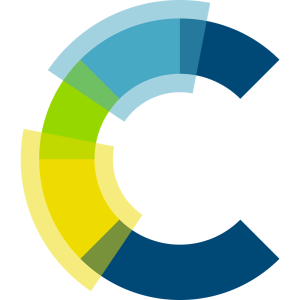
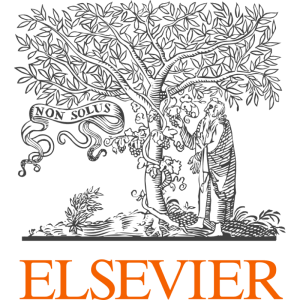
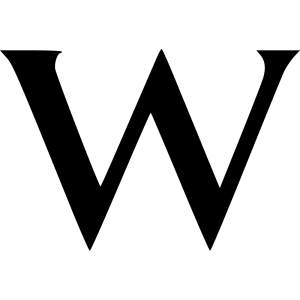
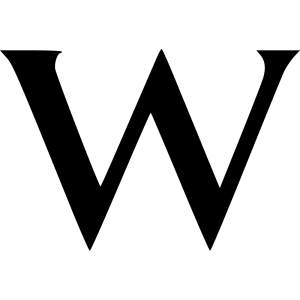
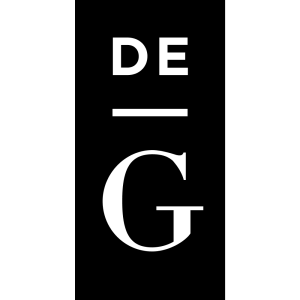
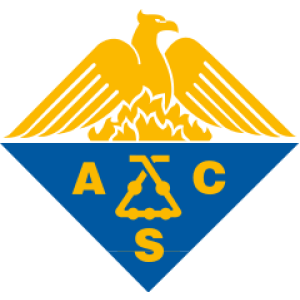
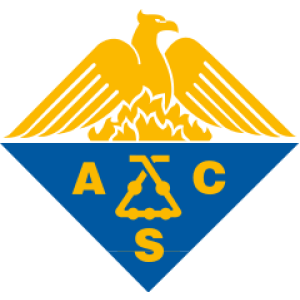
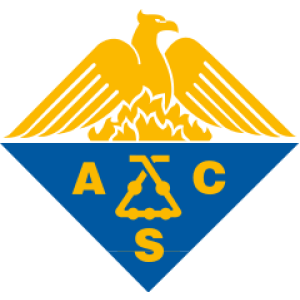