Keywords
Abstract
In today's world, environmental issues are becoming more and more pressing. The manufacture of structural materials such as metals, concrete, ceramics, and composites has a considerable impact on the environment. Therefore, the development and improvement of methods that minimize the adverse environmental impact and design of more sustainable production processes are fairly relevant. Currently, the concept of nature-inspired materials has been elaborated. A number of such materials have been already developed and some are being developed now. This review addresses, for the first time, the current state of research in the development of nature-inspired and safe materials based on titanium alloys and steels. The bibliography includes 144 references.
1. Introduction
The structural metal materials, including metal-based composites are used in a very broad range of human activities, e.g., in all transport vehicles, aerospace engineering, energy generation, mining industry, construction industry, road transport infrastructure, household appliances, agriculture, food production, as well as medicine, including implants and medical devices.
The required mechanical and performance characteristics of modern structural metal materials is attained by alloying. In particular, alloying elements such as Ni, Cr, Co, and V are often used in iron-based structural steels and alloys. Coatings based on Zn, Ni, Cr, and Cu are widely utilized to protect structural steels from corrosion. Corrosion-resistant steels are obtained by using high levels of alloying (above 13 mass %), most often, with Cr and Ni. Especially high contents of Cr (more than 14 mass %) and Ni (more than 10 mass %) are characteristic of alloys meant for operation at elevated temperatures. High-strength titanium- and aluminium-based alloys also have high corrosion resistance. The rate of corrosion of titanium alloys in seawater does not exceed 0.0001 mm per year, while for aluminium alloys, the corrosion rate is 0.007 mm per year. The required strength characteristics of structural titanium alloys are providing by adding alloying elements such as Al (not more than 6.5 mass %), V (not more than 16 mass %), and Cr (not more than 6 mass %). In the structural alloys based on aluminium, Cu, Ni, Cr, and Zn are widely used as alloying elements.
However, ions of all of the above alloying elements are able to diffuse from the materials to the fluid media of living organisms occurring in contact with them, as a result of chemical or electrochemical reactions of metals with the environment, or they can enter the environment as debris, particles, and dust as a result of corrosion, wear, and damage to parts and mechanisms, as well as during the production of alloys and alloy products.
The lifecycle of metal materials is composed of ore mining and refining, metal smelting, production of alloys, manufacturing of products, the use of products, and waste management. During waste management, it is possible to recycle the material into the starting alloy. At any of these stages, various heavy metals such as Ni, Cr, Al, and V can be discharged into the environment .[1-5]
As a result, these compounds accumulate in the environment and enter plants, animals, and human body from air, food and water, in particular via absorption through skin.[6-11] The most hazardous elements for the human body are Ni, Cr, Al, and V. The key problem is strong multi-faceted toxic action of these elements on humans, animals and plants.[12-17] Nickel and chromium are carcinogenic. The toxicity of chromium depends on the oxidation state. Particularly, Cr(VI) is almost a thousand times more toxic than Cr(III), because it is able to penetrate into living cells of animals and plants and induce a variety of cell damage, including DNA damage, chromosome aberrations, and changes in the epigenome.[18] Chromium(VI) anions are structurally similar to sulphate and phosphate anions; therefore, cells easily capture Cr(VI) ions by non-specific anion transporters. The consequences of chromium toxicity include decrease in the seed germination capacity, plant growth retardation, reduction in crop yields, inhibition of enzymatic activity, weakening of photosynthesis, oxidative imbalance, and genetic mutations in plants as well as some harmful diseases in animals and humans.[4], [18] The effect of nickel contamination on the marine fauna has been studied in relation to Japanese medaka. The study showed that nickel increases the oxidative stress and induces changes in metabolic processes.[5]
The vanadium toxicity is also considerably variable depending on the oxidative state: pentavalent vanadium is the most toxic and active vanadium species. Being an important raw material, it is an integral part of the steel industry. The environmental pollution by vanadium is mainly caused by mining of various vanadium-containing minerals leading to contamination of water, soil, and air. High concentrations of vanadium in soil and water may give rise to chlorosis, a plant disease associated with disruption of chlorophyll synthesis and decreasing activity of photosynthesis. As a result, the plant growth is retarded, root systems are reduced, and the nutritional quality of the crops is deteriorated.[1] The vanadium-containing particles carried by air were found to affect the human body by increasing the risk of development of various pathologies such as hypertension, arrhythmia, systemic inflammation, hypercoagulability, cancer, and bronchial hyperresponsiveness.[19]
The pressure aluminium die casting process also contributes to several environmental issues related to emissions to air, soil, and water. In particular, this is concerned with the formation of wastes such as aluminium dross produced during melting or ceramic lining waste from the furnaces.[2] Aluminium ions entering the environment and living organisms are hazardous for animals, plants, and humans.[19-21] Aluminium decreases the resistance of organisms to external infections, in particular, it reduces the time of survival of red blood cells and affects the cellular metabolism. Excess aluminium in soil leads to a drop in grain yield. When rainwater enters soil and clay, aluminium is washed away and consequently gets into brooks and lakes. This gives rise to the whole range of aberrations in the root meristem cells, that is, genome, chromosome and chromatid aberrations.[22] Study of the effect of aluminium salts on wild animals demonstrated that aluminium induces the formation of toxic oxygen-free radicals in the cells and indirectly influences lipid oxidation. This results in serious damage of DNA molecules. In the case of prolonged exposure, other effects have also been observed, e.g., changes in metabolic processes.[3]
In the contemporary world, environmental issues are becoming more and more pressing. The manufacture of structural materials such as metals, concrete, ceramics, and composites has a considerable impact on the environment. Therefore, it becomes very important to develop and improve approaches that would minimize the adverse impact on nature and to design more sustainable production processes.
Intensification of the processing of wastes of Cr-, V-, Ni-, or Al-containing alloys and increase in the resource and energy efficiency of chemical engineering systems using such alloys are also faced with additional problems and difficulties, some of them being expensive.[23-25] This requires development of new techniques for waste treatment and for recovery of metals such as Cr, V, Ni, Al, and other.
It should be specially emphasized that abandoning of using high-quality structural materials with high performance characteristics is incompatible with further progress of the humankind. Currently, the concept of nature-inspired materials has been developed.[26-35] This concept should help to overcome the above global challenge of the 21st century and provide for the sustainable development of civilization. This approach would help to arrange a harmonious communication between humans and the surrounding world and would favour building of a nature-inspired technosphere in sympathy with nature.[36][37]
An essential possible approach to implement the concept of nature-inspired technosphere is the design of a conceptually new generation of structural alloys and composites that meet a several conditions: (1) complete absence of the above toxic alloying elements or, at least, noticeable decrease in the content of these elements; (2) good corrosion resistance, which also decreases the environmental pollution; (3) high set of mechanical and performance characteristics; (4) better biocompatibility; (5) the absence of initiation or even the presence of inhibition of the formation of microorganisms pathogenic to humans and animals on the material surface.
A number of materials of this type have already been developed or are being actively developed. In this review, we consider for the first time the current state of development of nature-inspired and safe materials in the field of titanium alloys and steel.
2. Promising environmentally friendly and nature-inspired titanium alloys based on the Ti – Nb, Ti – Nb – Zr, Ti – Nb – Ta, and Ti – Nb – Ta – Zr systems
Titanium is non-toxic and does not form harmful oxides or nitrides, which makes it ideal material for implants, medical devices, and other articles that can be in contact with human body. However, pure titanium has low mechanical characteristics; therefore, titanium alloys are used to manufacture the products.
Titanium alloys can be classified in terms of their phase composition, particularly into α-alloys, the structure of which is formed by the α-phase; pseudo-α-alloys formed by the α-phase and a minor amount of the β-phase (not more than 5 mass %); (α + β)-alloys represented by both α- and β-phases; pseudo-β-alloys consisting of the β-phase and a minor inclusion of the α-phase; β-alloys with the structure formed by thermodynamically stable β-phase; and intermetallic-based alloys. The properties of α-alloys include high heat resistance, oxidation stability, moderate strength, and low processability (Table 1).[38-45] Pseudo-α-alloys also have high heat resistance and higher strength and ductility than α-alloys. α + β-Alloys have a balanced strength, ductility, and thermal hardening (quenching + ageing), but moderate heat resistance. Pseudo-β-alloys are characterized by high strength after ageing, good processability, but moderate heat resistance. Finally, β-alloys have the highest strength after ageing, high corrosion resistance, but low heat resistance and the lowest Young’s modulus.[46]
Titanium alloys possess unique properties such as high strength, corrosion resistance, biocompatibility and lightweightness (see Table 1).[47] Owing to high corrosion resistance, titanium alloys can operate at high humidity in harsh environments. Titanium alloys are fairly processable and can be easily treated by various methods, which makes it possible to manufacture products with intricate shapes and designs. In combination with high strength, this feature provides for using these alloys in the aerospace industry. the Ti – 6 Al – 4 V alloy and similar VT6 alloy manufactured in Russia are the most vivid examples of titanium alloys used in the aerospace, marine, and motor vehicle engineering, chemical engineering, and medicine.[48-54] The well-known shape memory alloy Nitinol (titanium nickelide) has high strength characteristics (800 – 1000 MPa), ductility of up to 50%, shape memory effect, and superelasticity.
Examples of high-strength structural titanium alloys used in aerospace industry include highly processable VT47 pseudo-β-alloy in the Ti – Al – Mo–V – Cr – Fe alloying system containing yttrium microadditive, VT23 and VT22 α + β-alloys, and VT14 alloy (see Table 1).[39-41][55-58] The PT-3V titanium alloy was designed for the fabrication of large welded structures operating in seawater, in particular for deepwater equipment, marine engineering structures, hull structures, propulsion systems, onshore and offshore pipelines, heat exchangers, etc. The PT-3V and 3M grades are used in mechanical engineering, and the alloy grades used in the energy generation industry are PT-1M and PT-7M.[56-58] 56 – 58
Thus, the currently used titanium alloys have good mechanical characteristics, but contain harmful alloying elements such as Ni, V, Cr, and Al; this can be adverse for the environmental safety and also prevents the use of these alloys in medicine. Regarding their application as implant materials, the existing titanium alloys have restrictions caused by the presence of toxic elements and too high elastic modulus (above 100 GPa). High toughness of these alloys may cause stress-induced crevice corrosion in the materials and mechanical mismatch between the bone and the implant (stress-shielding effect), resulting in considerable complications such as displacement of the implant relative to the bone, which requires repeated surgery.[59] In order to mitigate the stress-shielding effect, the Young’s modulus of the material used to manufacture implants should be as close as possible to the Young’s modulus of bone tissue (10 – 30 GPa).[60]
This has stimulated the development and implementation of new titanium alloys free from Ni, V, Cr, and Al. First of all, such alloys are meant for medical purposes. An example is provided by β-titanium alloys with a unique set of properties, which makes them promising for the use as implants and other medical appliances, particularly low Young’s modulus (less than 50 GPa) close to that of bone tissue, high strength (more than 500 MPa) combined with a low density to ensure low weight of the implant, high corrosion resistance, and enhanced biocompatibility, including the absence of allergic reactions.[61-65] In these alloys, the conventional alloying elements (Ni, V, Cr, and Al) are replaced by Nb, Fe, Mo, Ta, Hf, and Zr. These elements possess favourable bioneutrality characteristic of pure titanium.[65][66] The alloying with Nb improves the corrosion resistance, biocompatibility, and processability; the introduction of Zr and Mo enhances the mechanical characteristics, while Ta is a β-stabilizer [60][67-69] possessing the highest biocompatibility.[70][71]
The alloying with the above elements provides the production of both α + β alloys and β-alloys that possess the strength and ductility similar to those of the conventional type VT6 titanium alloy (σB up to 1350 MPa, δ up to 20%), but lower Young’s moduli. The addition of non-toxic elements that stabilize the β-phase (Nb, Zr, Ta, Mo) makes it possible to obtain metastable* β-titanium alloys that are not harmful to the human body and have a low elastic modulus (up to 80 GPa).[70]
The alloys formed in the Ti – Nb – Ta, Ti – Nb – Zr, Ti – Nb – Ta – Zr, and Ti – Nb systems possess a good set of mechanical properties (Table 2), including low Young’s modulus[60] [72-74] and shape memory effect or superelasticity, which makes them promising for implantology.
Alloys of the following compositions have been studied: Ti – (10/16/22)Nb,[75] Ti – 35Nb – 5Ta – 7Zr,[76] Ti – 38.3Ta – 22Zr – 8.1Nb, Ti – 38.9Ta – 25Zr – 5Nb, and Ti – 39.5Ta – 28Zr – 2.5Nb (Ref. [77]) (numerals in the composition indicate the contents of alloying elements in mass %); other alloys are also indicated in Table 2. Some of these alloys possess good mechanical properties and corrosion resistance. The latter is due to the fact that the elements form a passive protective layer with good adhesion on the surface of manufactured items.[62] [78] Generally, the new titanium alloys have the following mechanical characteristics: Е = 15.3 – 85.2 GPa, σ0.2 = 188 – 1107 MPa, σB = 490 – 1602 MPa, δ = 1.2 – 21%; some of them are inferior to the conventional alloy in the mechanical strength, while others are comparable with or superior to the conventional alloy. For example, Ti – Ta – Zr – Nb alloys have high tensile strength and yield strength, which are much higher than those of the conventional Ti – 6 Al – 4 V alloy.[77]
A number of alloys with a low Young’s modulus (below 50 GPa) have been developed in the Ti – Nb – Ta, Ti – Nb – Zr, Ti – Nb – Ta – Zr, and Ti – Nb systems (see Table 2);[73][74] [79-84] currently, this is the closest approximation to human bone characteristics. A unique value of the Young’s modulus (15.3 GPa) perfectly corresponding to that of the human bone, was found for the Ti – 35 Nb – 5 Ta – 7 Zr alloy;77 however, the lack of data precludes comprehensive evaluation of the results. Comparison of the mechanical properties of some existing and newly developed titanium alloys shows (Fig. 2) that the new alloys are not inferior in their properties to the currently used ones containing toxic alloying elements. Alloys with desired performance characteristics can be selected for a specific application. The absence of toxic elements in the new alloys, all other characteristics being the same, makes the use of these alloys preferable.
Studies of the considered titanium alloys demonstrated that the lowest Young’s moduli (15.3 – 50 GPa) were attained for the following alloys: Ti – 20 Nb – 13 Ta – 5 Zr, Ti – 15 Nb – 5 Ta, Ti – 15 Nb – 10 Ta, Ti – 20 Nb – 5 Ta, Ti – 20 Nb – 7.5Ta, Ti – 20Nb – 10Ta, Ti – 20Nb – 10Ta – 5Zr, Ti – 25 Nb – 13 Ta – 5 Zr, and Ti – 30 Nb – 10 Ta – 5 Zr (at.%) and Ti – 35 Nb – 5 Ta – 7 Zr (mass %).
Thus, a new generation of innovative environmentally friendly titanium alloys is being actively developed. These alloys can be called nature-inspired, as their mechanical characteristics are quite close to the characteristics of human and animal bone tissue and their alloying elements are safe for humans even when the alloys are placed inside the body. It is noteworthy that the mechanical characteristics of the new alloys not only imply their application for biomedical purposes as structural materials, but also make them potentially competitive for the use in high-tech industry branches.
* Stable β-titanium alloys are based on the stable β-phase, which does not decompose under load or on heating; metastable β-titanium alloys are alloys in which the β-phase can decompose under stress or on heating.[85]
3. Nickel-free corrosion-resistant austenitic structural steels
Recent decades have witnessed a noticeable increase in the attention to nickel as a source of environmental pollution. This is caused by increasing production output and expansion of the scope of application of nickel. According to the data for 2022, about 65% of the global output of nickel, which amounts to 2015 thousand tons, is used for the production of corrosion-resistant steels.[88] Most of these steels are austenitic steels with nickel content ranging from 8 (08Kh18N10, AISI 304) to 18% (20Kh23N18, AISI 310).[89] The increase in the nickel concentration in air, water, soil, and foodstuff may be harmful for human health.[90]
The common corrosion-resistant austenitic steels such as 12Kh12N10T, 05Kh18N12, or 316L contain 12.0 – 15.0% nickel, which, being accumulated in the body, may give rise to pulmonary fibrosis and cardiovascular and renal diseases. There are data that high content of nickel ions in tissues may cause genotoxic and mutagenic effects.[91] Thus, it becomes highly important to design austenitic steels that are either free from nickel or contain a minimum amount of nickel and combining high mechanical properties and corrosion resistance. The design of these steels is underway at top physical metallurgy centres in developed countries. A special place among these materials belongs to nitrogen-containing austenitic steels.[92]
The first systematic studies dealing with the design of nitrogen-alloyed steels date back to the 1960s and 1970s.[93-95] Table 3 summarizes the main mechanical properties of high-nitrogen (containing more than 0.5% nitrogen) austenitic steels, 02Kh20AG14N8MF, 02Kh20AG12N4, 05Kh20A10N3AMF, and 02Kh20AG10N4MFB, and conventional austenitic steels, 08Kh18N10 (AISI 304) and 03Kh17N14M3 (AISI 316L). It can be seen that nitrogen-containing steels are significantly superior to conventional steels in the strength and impact toughness, while being virtually equal to them in terms of ductility.[96-98]*
It is important that the desire to minimize the nickel content or even totally eliminate nickel is due, to a large extent, to economic reasons, that is, poor resource base and high cost of nickel. Another reason for limiting the nickel concentration is related to its adverse effect on the nitrogen solubility in steel. Like other austenite-forming elements such as cobalt and copper, nickel markedly decreases the nitrogen solubility. The only austenite-forming element that increases the solubility of nitrogen in the iron matrix is manganese. This initiated the development of high-manganese nickel-free nitrogen steels. An example is the 12Kh18AG18 steel,[99] an analogue of the P900 austenitic steel, which contains up to 0.7% nitrogen, in addition to 18% chromium and manganese. This steel is used to manufacture shroud rings of power generators andб owing to its ability to be hardened under cold working and intense dynamic load, while maintaining fairly high ductility and toughness, it is considered as a promising armour material.[100]
However, steels with high manganese contents have several significant drawbacks. An increase in the manganese concentration in chromium–manganese nitrogen-alloyed austenitic steels leads to increasing temperature of existence of the σ-phase;[101] manganese in concentrations of 10 – 14% decreases the stacking fault energy (SFE) of austenite in nitrogen-alloyed steels and, as a consequence, decreases the resistance to strain-induced martensitic transformation. In contrast, the simultaneous increase in the manganese and nitrogen concentrations leads to a negative volume effect of the strain-induced martensitic transformation, accompanied by appearance of tensile stress. The above effects may result in a considerable decrease in the performance characteristics of steels, such as non-magnetization, ductility, fracture toughness, fatigue strength, and weldability.[102][103]
On the other hand, high manganese content in steel has an adverse effect on human health and the environment during common and widespread operations such as welding and metal cutting. Welding aerosols containing manganese nanoparticles can cause serious damage to the nervous system.[104]
An alternative to the conventional methods for the fabrication of nitrogen-containing austenitic steels is the process of steel smelting and casting at an elevated pressure of nitrogen above the melt. This method makes it possible to attain a nitrogen content above equilibrium (unlike the equilibrium content resulting from crystallization of a melt at normal atmospheric pressure). Acknowledgment should be made of the design of counter-pressure casting units in the late 1970s.[105][106] Characteristic features of the formation of structural and phase state and physical and mechanical properties of this class of steels were identified. In particular, the kinetics of discontinuous decomposition of nitrogen-alloyed austenite to give pearlite-like chromium nitride colonies was investigated (Fig. 3).[107]
Further development of these studies resulted in the design of nitrogen-alloyed chromium steels containing super-equilibrium amounts of nitrogen (0.9 – 1.3%), but no nickel or manganese as alloying elements,[108] which are, therefore, much safer for humans and the environment. At the same time, high-nitrogen austenitic steels produced by electroslag remelting under pressure of nitrogen (pressurized electroslag remelting, PESR) were investigated.[109-111]
It is noteworthy that despite high mechanical properties and corrosion resistance, steels with super-equilibrium nitrogen contents have certain significant disadvantages. A unique feature of nitrogen austenite, absent in other metals with the FCC crystal lattice, is the presence of ductile-to-brittle transition. The transition temperature increases in proportion with the content of nitrogen [112] and for nitrogen contents above 1% in the absence of nickel, it may shift to positive temperatures. High nitrogen concentration leads to fast appearance of the discontinuous decomposition of nitrogen austenite in the temperature range of 500 – 1000°C, which considerably decreases the fracture toughness.[113]This brings about engineering difficulties for heat treatment, hot working, and welding of high-nitrogen austenitic steels.
The unfavourable effects of nickel ions in stainless steels stimulated the development of nickel-free austenitic steels for medical applications. Nickel is replaced with nitrogen, which provides stability of the austenitic structure and improves the properties of steel. Nickel-free stainless steels with high nitrogen content have high strength, ductility, corrosion resistance, and biocompatibility. An engineering drawback of steels with super-equilibrium nitrogen content is the complexity and high energy consumption during smelting. In view of the restrictions on the weight and size of ingots produced at the existing PESR units, the application area of these steels is for critically important structures operating at climatic temperatures, such as parts of power generators, medical products (implants, prostheses, etc.), and tools.[114] These and some other features should be taken into account in the development and application of austenitic steels containing nitrogen.[115]
Currently, active research of nitrogen-containing austenitic steels is in progress. Thus, broad range of studies has been carried out to elucidate the effect of heat treatment and hot working on the structure and mechanical properties of this class of materials [116-118] and the effect of severe plastic deformation.[119-121] The fatigue properties of high-nitrogen austenitic steels have been investigated.[122-124]
Chromium – manganese and chromium – manganese – nickel nitrogen austenitic steels are employed in military and icebreaker shipbuilding owing to their high strength, fracture toughness at low climatic temperatures, and corrosion resistance.[125-127] In particular, sparingly alloyed high-strength chromium –manganese 05Kh16G7AMF austenitic steel has been developed.[101] Another important application of high-nitrogen austenitic non-magnetic chromium – manganese – nickel steels with low nickel contents, P530, P550, and P580, is for manufacturing of non-magnetic heavy-weight drill pipes.
Thus, nitrogen-containing austenitic steels that do not contain Ni or contain a minor amount of Ni: a low Mn content should be considered as promising structural materials combining high physical and mechanical properties and corrosion resistance with lower economic and environmental costs of production and application than the conventional austenitic steels.
4. Corrosion-resistant steels with antimicrobial activity
Austenitic steels characterized by high corrosion resistance are extensively used in the fields where manufactured items and structures operate in contact with biologically active media, that is, in medicine, agriculture, veterinary medicine, food industry, household appliances, cosmetic products, river, marine and coastal facilities, heat exchangers, special pipelines, and equipment operating in a harsh tropical climate. Apart from the above-described VT6 titanium alloy, the 316L steel (or Russian analogues, 03Kh17N10M2 and 03Kh17N14M3) are commonly used for this purpose.[120-126] These steels usually have the following composition (mass %): C ≤ 0.03, Mn ≤ 2, Si ≤ 0.75, Cr ≈ 16 – 18, Ni ≈ 10 – 14, and Mo ≈ 1.5 – 3 and the following mechanical characteristics: σ0.2 = 170 – 300 MPa, σB = 485 – 580 MPa, δ = 40 – 60%, and Vickers hardness = 210 – 220 HV.
However, the use of products made of conventional grades of austenitic steels in biologically active media is accompanied by the adsorption of proteins and formation of hazardous biofilm on their surface, which leads to corrosion and appearance of a source of bacterial infection.[62], [128-132] To eliminate this problem, the material should possess antibacterial properties. It was shown that adding a small amount of silver as an alloying element to corrosion-resistant steels is expedient to endow them with the required antibacterial properties (Table 4).[133-135]
A problem associated with introducing of silver into alloys is the possible deterioration of mechanical properties of the whole material because of the plasticizing effect of this type of alloying and because of the possible liquation (inhomogeneous distribution of silver throughout the alloy). This problem is addressed by a variety of methods (e.g., smelting in induction furnace in a nitrogen atmosphere or argon-arc melting followed by homogenizing annealing), which provide homogeneous alloys, and some engineering solutions (e.g., repeated smelting with ingot turning followed by homogenizing annealing). In addition, the amount of added silver is minimized. Unfortunately, publications on this subject do not always provide full-scale testing results (or not all types of testing necessary for full-scale description of the developed alloys are conducted, Table 4); this precludes gaining the whole picture and drawing clear conclusions.
A study of the effect of 0.1, 0.2, and 0.3 mass % silver on the antimicrobial and antibacterial activity of corrosion-resistant type 304 steel, produced by induction furnace smelting in a nitrogen atmosphere, showed the presence of antibacterial activity of the silver-alloyed steel against Staphylococcus aureus and Escherichia coli (see Table 4).[131] The addition of 0.03 and 0.09 mass % Ag to type 316 steel increased the antibacterial activity against Escherichia coli, with the bacterial inhibition rate being 89.9% and 98.0%, respectively.[132] The bacterial inhibition activity of the duplex 2205 stainless steel doped with 0.2 mass % Ag was 100% against Escherichia coli and 99.5% against Staphylococcus aureus.[133]
The conducted studies indicate that addition of a small amount of silver (0.03 – 0.5 mass %) to steel increased the antibacterial activity against various bacteria, which can be as high as 100%.
Quite recently, the addition of 0.2 and 0.5 mass % silver to the 03Kh17N10M2 steel, which is an analogue of 316L steel, has been studied.[134-139]* Steel samples as 1 mm-thick sheets were obtained by argon-arc melting followed by homogenizing annealing and stepwise rolling preceded by heating up to 1100°C. Silver was uniformly distributed throughout the samples. Steels containing 0.2% Ag had 100% antibacterial effect against Pseudomonas marginalis and Clavibacter michiganensis, while steels with 0.5% Ag added showed 100% antibacterial effect against Xanthomonas campestris, Erwinia carotovora, and Clavibacter michiganensis. An increase in the silver content induced a slight increase in the ductility and decrease in the strength and Vickers hardness, but in general, the mechanical characteristics of all samples corresponded to the ASTM standard (see Table 4).[140]
In recent years, additive manufacturing techniques (3D printing) have been actively developed. [141-143] Currently, parts made of printed titanium alloys (e.g., VT6) and stainless steels (e.g., 316L) are already used in various industrial applications. One of the challenges associated with this type of manufacturing is the quality of the starting material, which should ensure a compact 3D packing of particles upon a steady-state supply of the feed, which is usually a powder, the spherical geometry of which provides the required properties and which is either added layer-by-layer and melted on treatment with a source of energy or supplied directly to the point of printing.[144] To be used for additive manufacturing, powders should have a fluidity of less than 30 s for 50 g of the powder and a bulk density of more than 3 g cm–3.
Currently, there are numerous methods for the production of spherical powders: gas atomization, water atomization, centrifugal atomization, ultrasonic atomization, non-contact atomization, plasma spraying of a wire, plasma spraying of a rotating electrode, and plasma spheroidization.
Highly spherical powders with minimum defects were obtained by plasma spraying of a wire (Fig. 4).[134][135][139]
According to the studies, the fluidity of the resulting powders was, on average, 17.9 s and the bulk density was 3.76 g cm–3, and the addition of silver did not influence the mechanical characteristics, which is important for the subsequent manufacture of the final products. The silver content in the powders corresponded to the initial silver content in steels. Study of the hardness of ingots, plates, and powder particles showed that the hardness decreased with increasing silver content, which is attributable to the introduction of a softer component into the corrosion-resistant steel (Table 5).
Study of the mechanical properties of plates and wires made of these steels showed that the addition of 0.2 mass % Ag to the steel has little effect on the strength and ductility characteristics, while the addition of 0.5 mass % Ag leads to a slight decrease in the yield strength. Measurements carried out for a wire indicated an increase in the strength characteristics.
The formation of steel billets in the form of ingots, sheets, wires, and powders and the production of finished products occurs under high temperatures. For example, in the production of spherical powders, the plasma jet temperature can reach 3000 – 5000°C, which is much higher than the melting point (962°C) and the boiling point of silver (2167°C). Therefore, if the distribution of silver in the initial melt is non-uniform, silver can burn-off from the melt. Therefore, it is very important to achieve a uniform distribution of silver throughout the alloy.
The addressed studies indicate that all raw materials (both plates and 3D printing powders obtained from them) possessed antibacterial activity. It is still to be verified whether the antibacterial properties are retained in the final products.
*see Table 4
5. Conclusion
Currently, the production output of metals and alloys containing toxic elements is more than two billion tons per year.* The huge amount of waste formed in this branch of industry during mining, production, and processing gives an idea of the total damage to the environment caused by this industry. However, structural metal materials are needed for a wide range of applications (transport, energy generation, construction, medicine, etc.), and human civilization is currently impossible without them. Therefore, the modern trends in the development of structural materials are directed towards designing of environmentally friendly alloys with high performance characteristics and minimized harmful impact on the environment and human health (Fig. 5).
The key lines of research are as follows:
(1) design of new β-titanium alloys, environmentally safe materials alloyed with bioinert elements (Nb, Ta, Zr, Mo). A number of newly developed alloys that are currently being studied possess low elastic moduli similar to that of the bone tissue, high strength, and excellent corrosion resistance, which makes them suitable for medical implants and other high-tech applications;
(2) design of nitrogen austenitic steels alloyed with nitrogen instead of nickel. The new steels demonstrate high strength, corrosion resistance, and economic feasibility. They are promising for the use in shipbuilding, medical devices, and other critical structures. However, the restrictions related to the production complexity and effect of high concentrations of nitrogen on the mechanical properties are retained. Therefore, the use of toxic alloying elements cannot yet be completely abandoned;
(3) design of antibacterial austenitic steels, which acquire antibacterial properties against a broad range of pathogens upon the addition of silver (0.03 – 0.5 mass %), while retaining the corrosion resistance and mechanical reliability. The use of these materials is in high demand in medicine and food industry. The production difficulties associated with the uniform silver distribution and high-temperature treatment are partially solved by using modern smelting and rolling techniques. Studies of alloys composed entirely of non-toxic elements are now underway (these data are being prepared for publication at the moment).
The above lines of research reflect the transition to environmentally friendly and highly efficient technologies and nature-compatible or nature-inspired materials. The key prospects include further improvement of production methods, development of additive technologies and scaling up of the production of safe alloys for wider applications.
This review was written with the financial support of the Russian Science Foundation (grant No. 21-79-30 029).
* https://pubs.acs.org/doi/full/10.1021/acs.chemrev.2c00799 According to the data of the World Steel Association (WSA), the global production output of steel in 2023 was 1.88 billion tons, which is virtually equal to that of 2022 (minus 0.1%) (https://mashprom.ru/press/news/proizodstvo-stali-v-rossii-i-mire-v-2023-godu/). In Russia, this value was 75.8 million tons (https://vtorion.ru/blog/article/mirovoe-proizvodstvo-stali-v-2023-godu/).
References
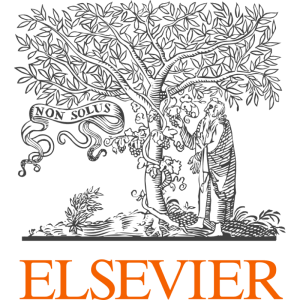
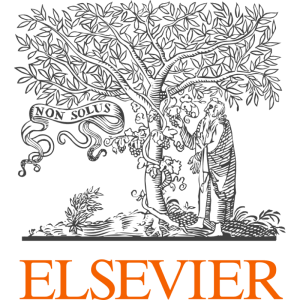
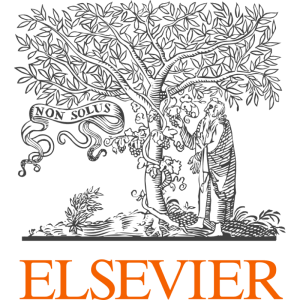
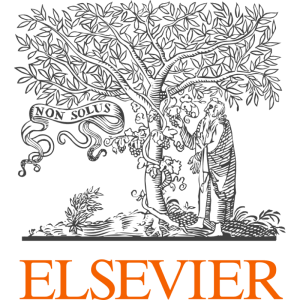
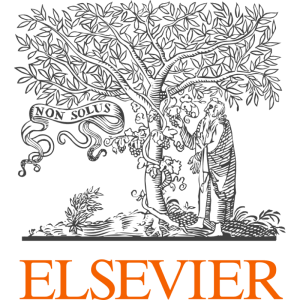
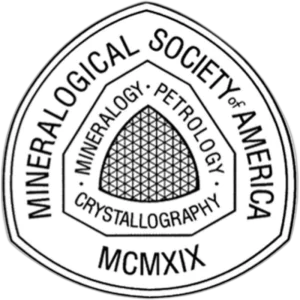
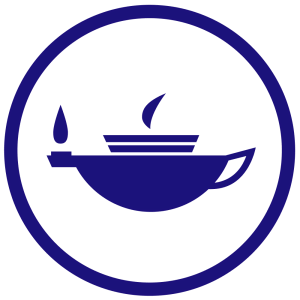
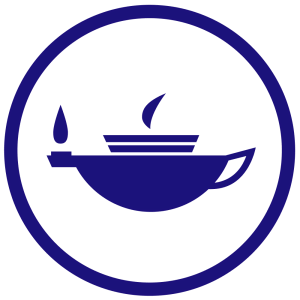

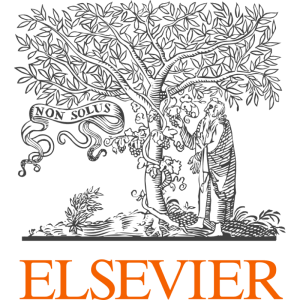
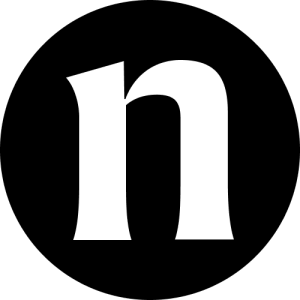
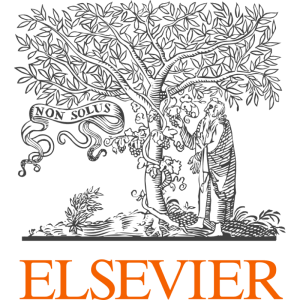
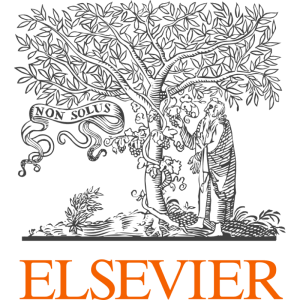
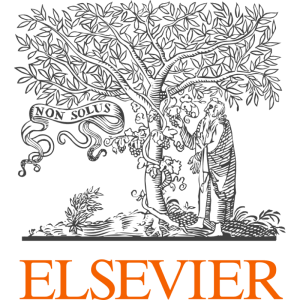
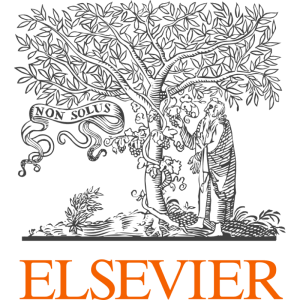
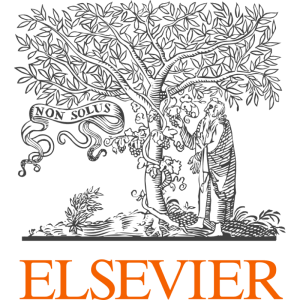
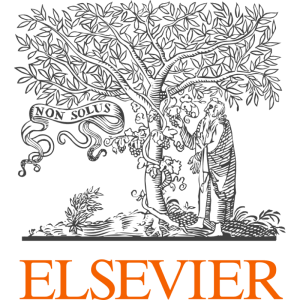
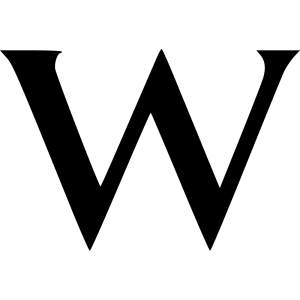

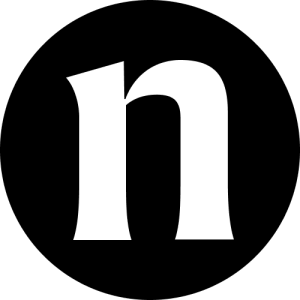
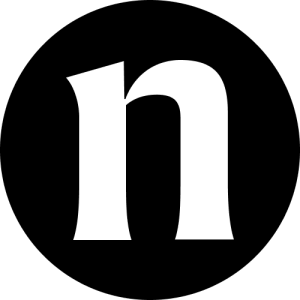
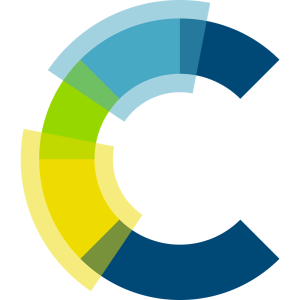
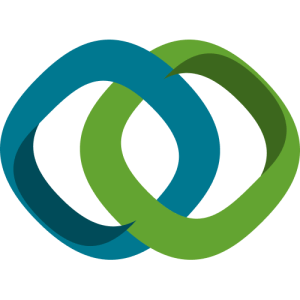
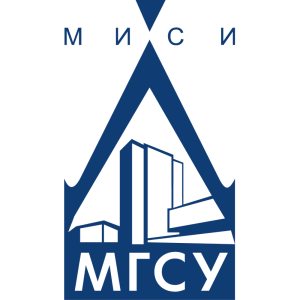
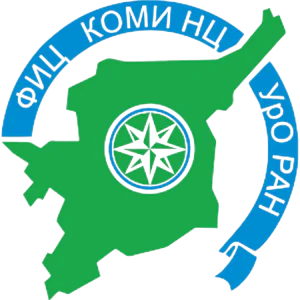
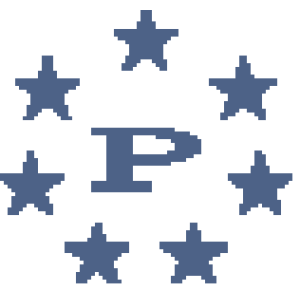
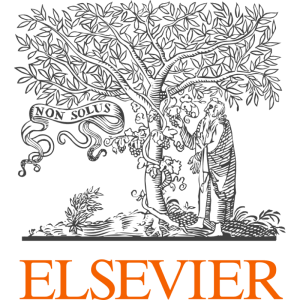
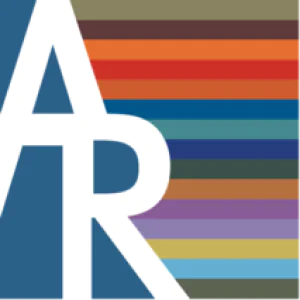
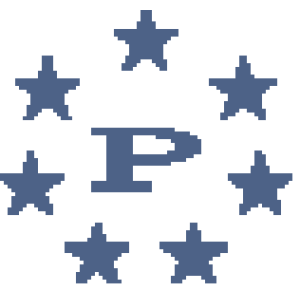
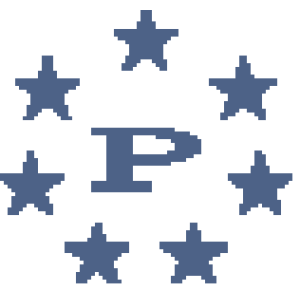
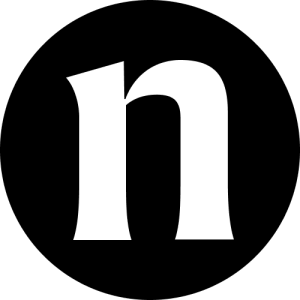
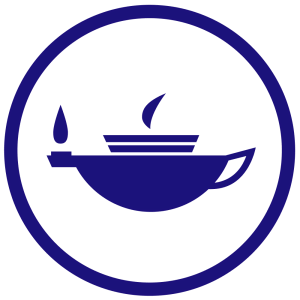
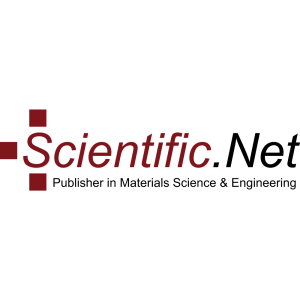
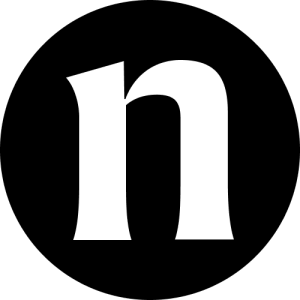
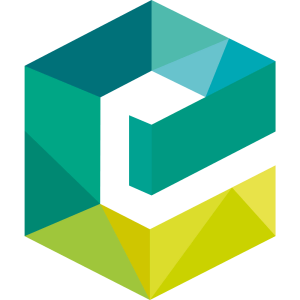
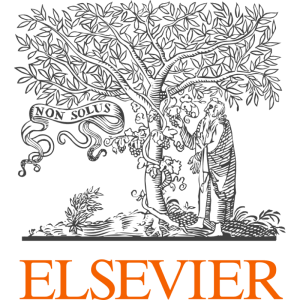
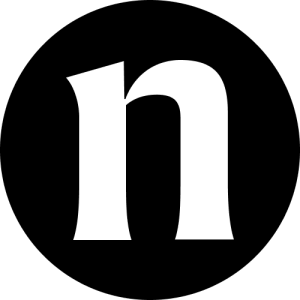
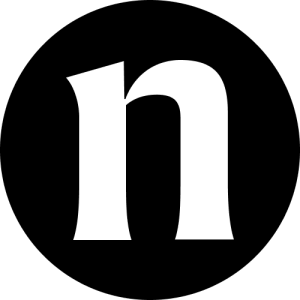
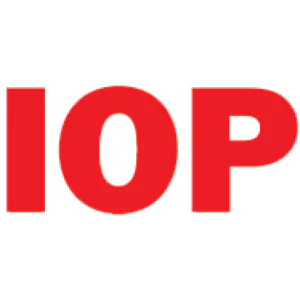
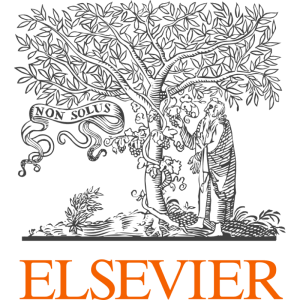
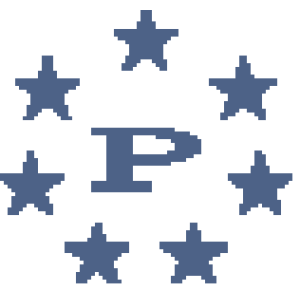
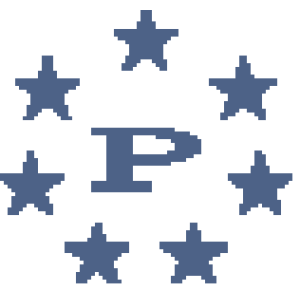
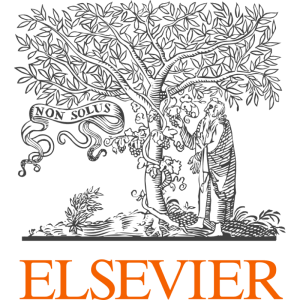
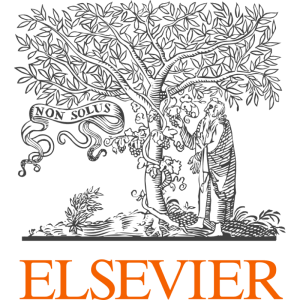
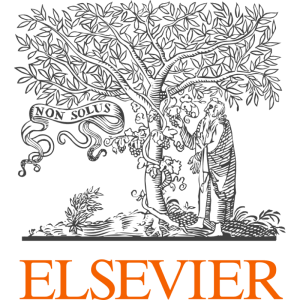
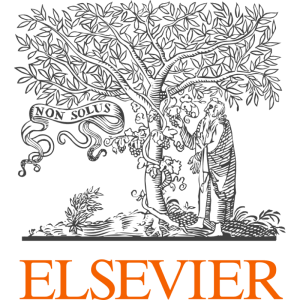

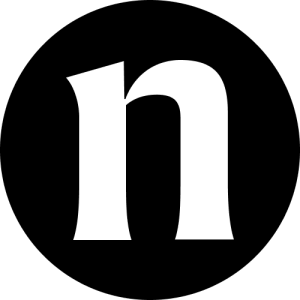
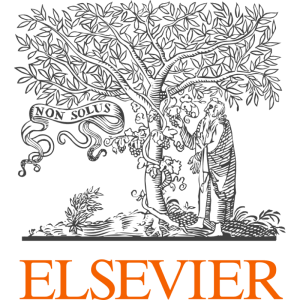
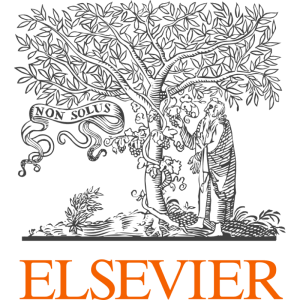
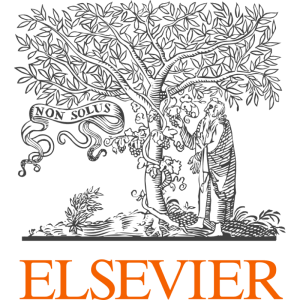
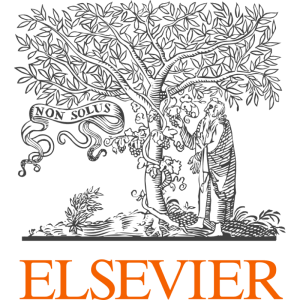
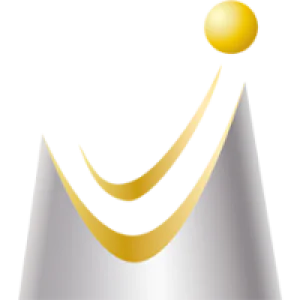
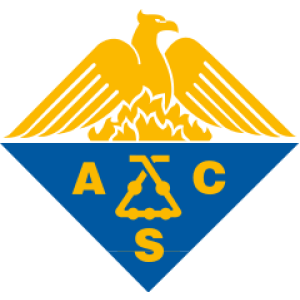
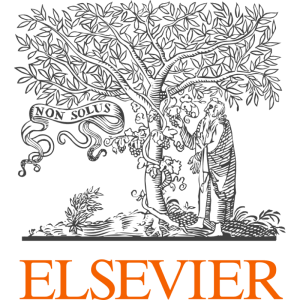
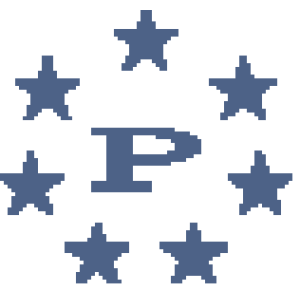
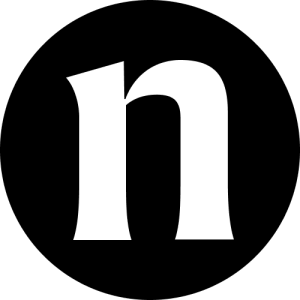
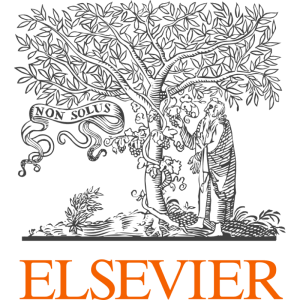
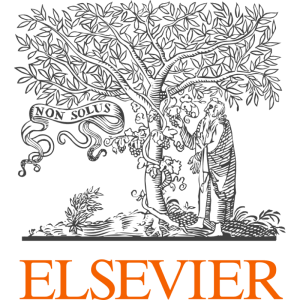

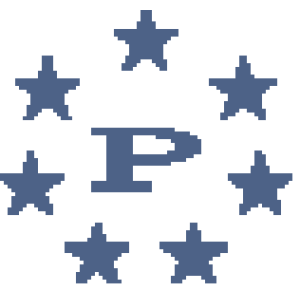
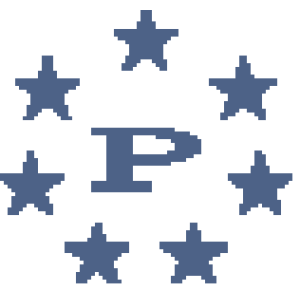

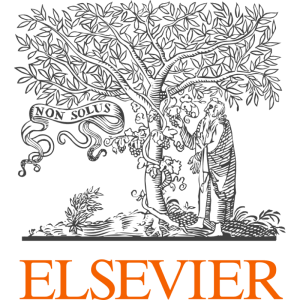
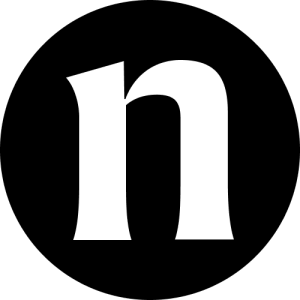

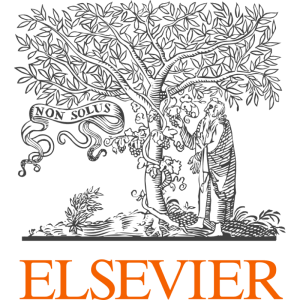
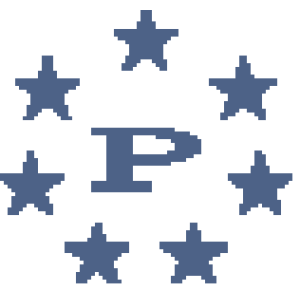
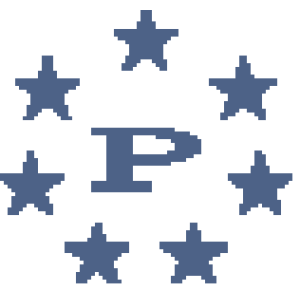
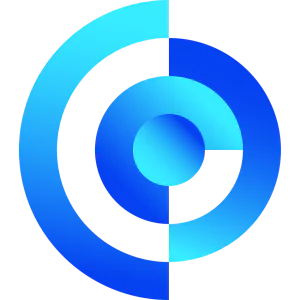
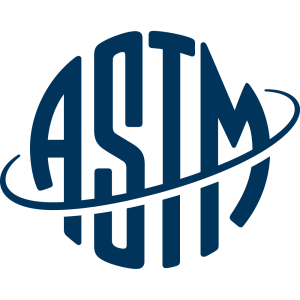
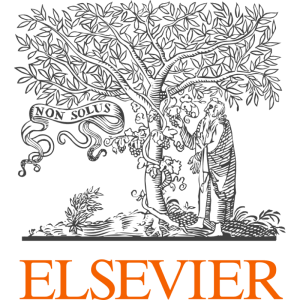
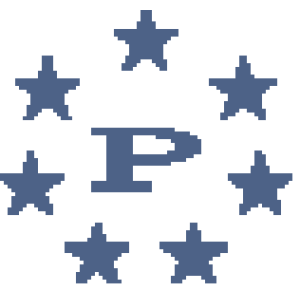
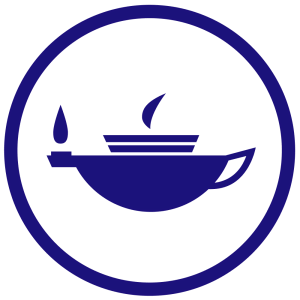
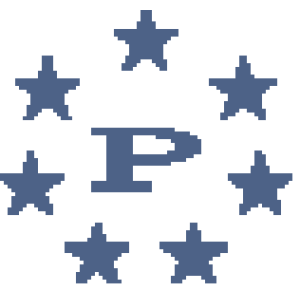
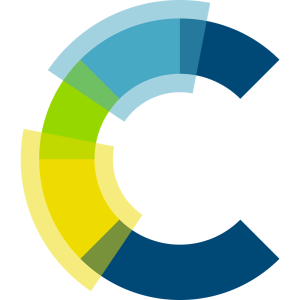
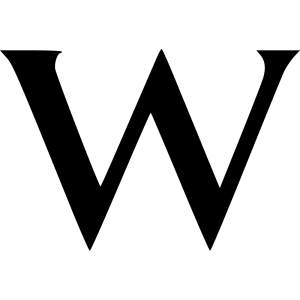
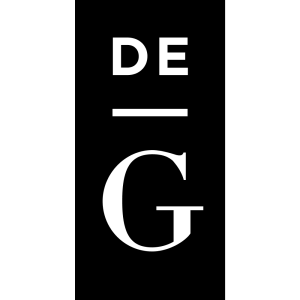
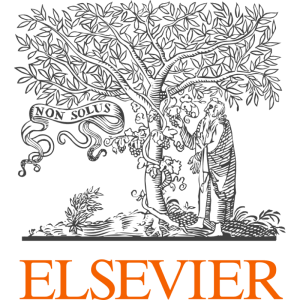
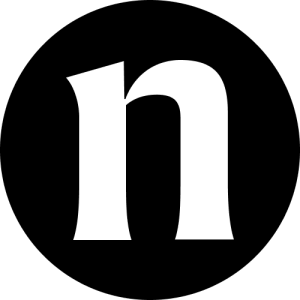
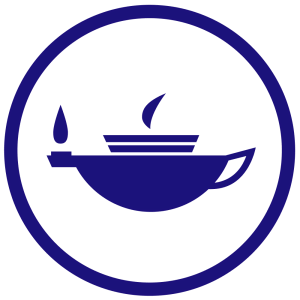
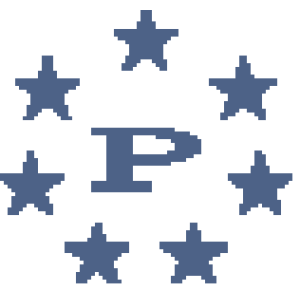
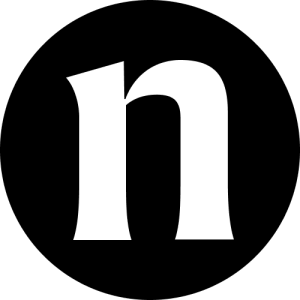
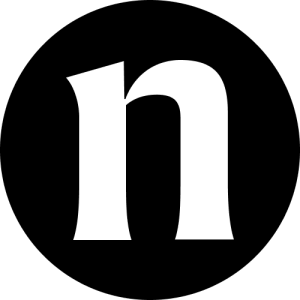
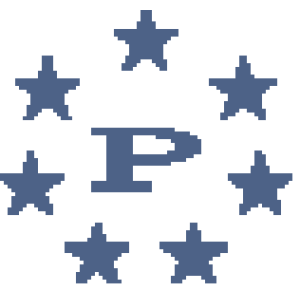
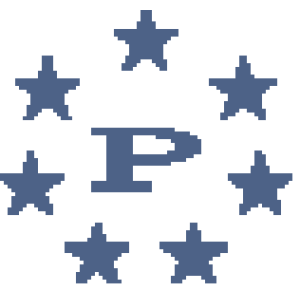
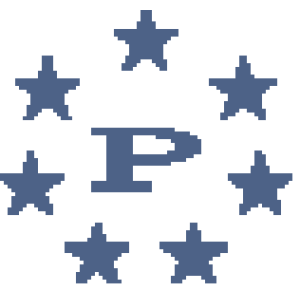
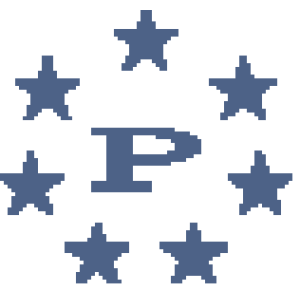
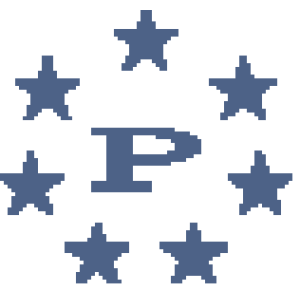
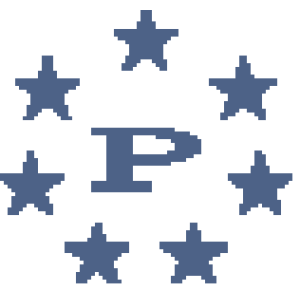
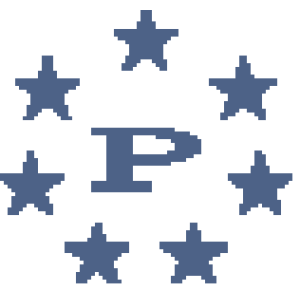
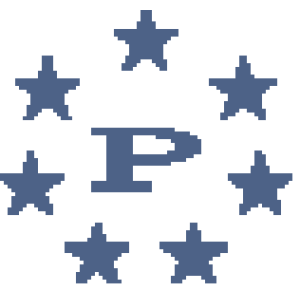
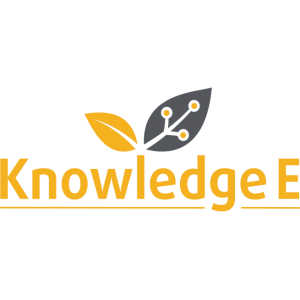
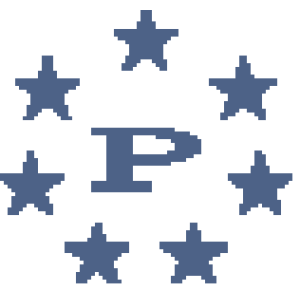
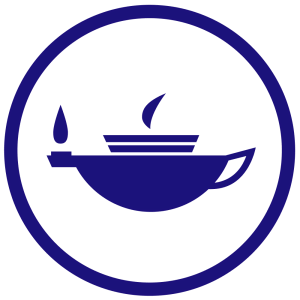
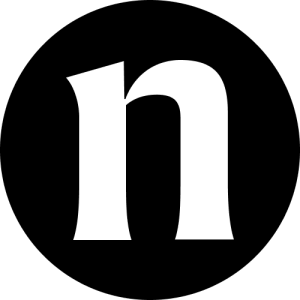
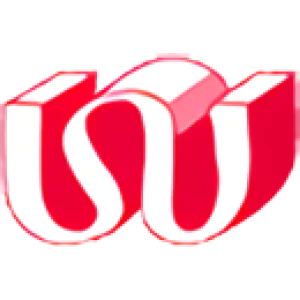
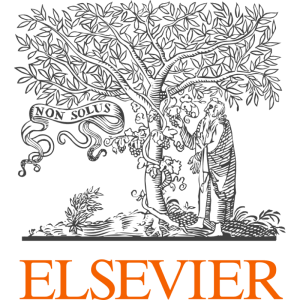
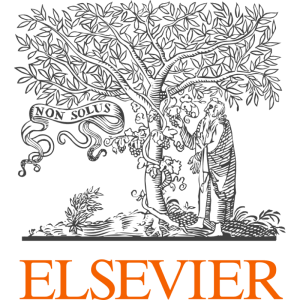
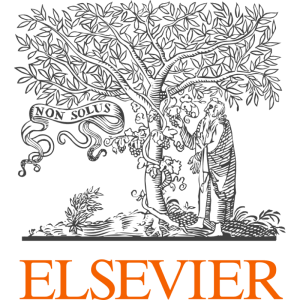


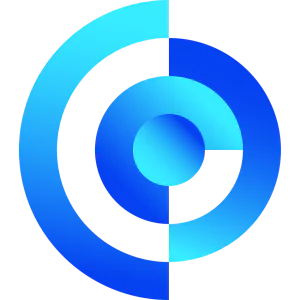
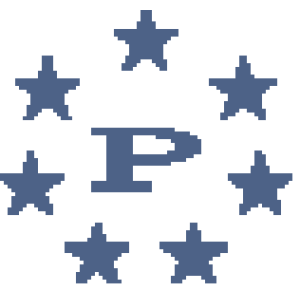
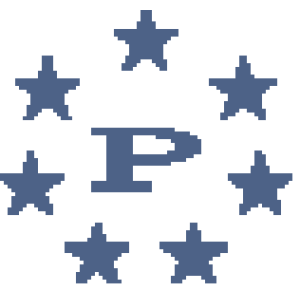
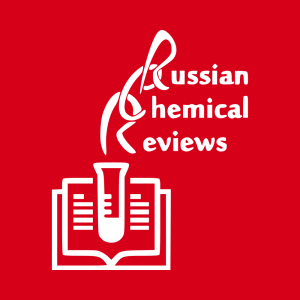
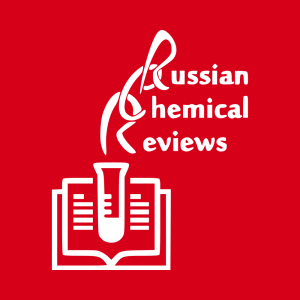
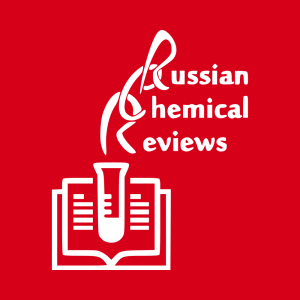
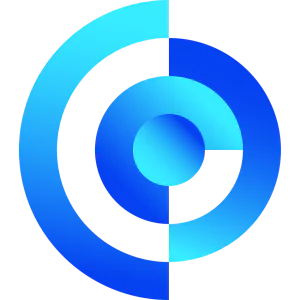