Keywords
Abstract
The application of additive technologies to the manufacture of polymer and composite products is now actively expanding. The FDM printing process is popular because of its ability to adapt to specific tasks and to bring products with complex geometries into production quickly and at minimal cost, and is seen as a technology that can compete with injection molding. However, due to the nature of the process, FDM printed parts are significantly inferior in quality to injection molded parts. Much attention is now being paid to research into supplementary treatment methods to improve the properties of FDM printing parts. However, there is no complete and clear description of such methods, nor are there any recommendations on the choice of treatment methods aimed at improving the specific parts properties. The aim of this review is to analyse the research in the field of post-treatment of parts in order to systematise their advantages and limitations, which will allow a more reasoned choice of a post-treatment method to improve specific properties of FDM printing parts.
The bibliography includes 120 references.
1. Introduction
Currently, the term additive manufacturing (AM) or 3D printing defines the technology used to create 3D/4D parts by layer-by-layer application of various materials such as polymers, metals, ceramics and composites[1-4]. Additive technologies are widely used to manufacture complex shapes that are difficult, and often impossible, to produce using traditional manufacturing processes in industries such as aerospace, automotive and biomechanics[1, 2, 5]. More recently, the use of 3D printing in chemistry and related industries (biochemistry, pharmaceuticals) has expanded to create devices and materials tailored to specific research problems[6].
AM technologies can be divided into the following groups: binder jetting; directed energy and material deposition; material extrusion including fused deposition modelling (FDM); material jetting; powder bed fusion; sheet lamination; vat photopolymerisation[7-15].
Of all the AM technologies and methods, FDM printing is the most widely used because of its ability to be easily customised and to bring complex geometry parts into production as quickly as possible at minimal cost.
A schematic of the FDM printing process is shown in Figure 1. During printing, the source material, in the form of a filament, is fed into the print head, which heats the material to a semi-liquid state above the glass transition temperature. It is then extruded from the nozzle and deposited onto the printer’s built platform (table). The solid filament fed from the spool acts as a piston, pushing the molten filament out of the nozzle[16, 17]. The force exerted by the filament to extrude the melt must be sufficient to overcome the pressure drop across the print head depending on the shape of the part and the rheological properties of the material. The print head or table moves in the X and Y axes to form two-dimensional layers of the part. As each layer is completed, the print head or table moves along the Z axis by the thickness of the layer, allowing the next layer to be applied on top of the previous layer. The nozzle tip pushes the molten material against the previous layer, which is re-melted, allowing the new layer to fuse with the previously printed layer. Once applied, the filament material hardens rapidly. The layer-by-layer application process continues until the part is printed completely.
Currently, another extrusion-based method is being developed for 3D printing polyamide and polyamide-based composite parts, using granules of the material rather than filaments (fused granulate fabrication, or FGF). A screw device, similar to the screw of an injection molding machine, is usually used to feed the material into the print zone and plasticization it[18-22]. Today, however, the granule printing method is not yet as widely used as the FDM method, so the number of studies on this method is small.
FDM is often seen as a technology that competes with the well-known method of manufacturing non-metallic products — injection molding. This issue is particularly relevant for small-scale and one-off manufacturing. From the point of view of initial model design, material costs, ease of making changes to the part geometry and the lack of need for specialized tooling (injection molds), FDM printing has undeniable advantages over injection molding. However, due to the specifics of the printing process associated with layer-by-layer build, printed parts are significantly inferior to injection molded parts in terms of strength and surface quality, minimizing the benefits of 3D printing.
Numerous studies have shown that FDM printed thermoplastic polymer and composite parts have inherent weaknesses that directly affect the mechanical performance and appearance of the finished product, which fall into two broad categories[23-26]:
— defects in parts due to deviating amounts of material (voids, threads, over- and under-extrusion, ribbing, bubbles and pores) or part deformation (shrinkage, warping, displacement of layers, delamination/weak bonding, twisting and cracks)[25, 26];
— characteristics inherent to the FDM printing parts: high surface roughness of the finished product, resulting, among other factors, from the stair-step effect (see Figure 1); anisotropy of the mechanical properties, strongly dependent on the printing direction.
Recently, a lot of attention has been paid to the research of various post treatment methods to improve the mechanical properties and surface quality of FDM printed parts.
The aim of this paper is to analyse current research in the area of supplementary treatment of FDM printed parts. The main focus is on the methods of post treatment in order to identify the applications and limitations of these methods.
2. Classification of supplementary treatment methods
At present, there is no complete and clear description of methods of supplementary treatment of FDM printed parts. Researchers, are usually limited to the description of processing technologies, consideration of individual properties of specimens (tensile and compressive strength, modulus of elasticity, yield strength, strains beyond yield strength, impact toughness, plasticity, hardness, porosity, etc.), and analysis of the results obtained. Consequently, no recommendations on the choice of supplementary treatment technology aimed at improving the properties of specific parts can be found.
The analysis of publications has shown that the methods of supplementary treatment can be divided into preparation before printing (pre-treatment), supplementary treatment directly during the printing process, and treatment after the part has been printed (post-treatment)[1, 2, 24, 27]. Figure 2 shows a scheme illustrating methods of supplementary treatment of FDM printed parts.
3. Pre-treatment methods
3.1. Improving the properties of the source material
The material for FDM printing is a thermoplastic filament, which is characterized by its infinite length in relation to its cross-section. The most commonly used thermoplastic polymers are:
More recently, the range of applications for FDM printing has been greatly expanded with the use of high-performance thermoplastics such as[27, 31, 32]:
Filaments are currently produced in diameters of 1.75 and 2.85 mm. In most cases, when using commercially available material, only pre-drying of the filament is used to improve its properties[28, 30].
Recently, composite materials based on thermoplastic matrices have been increasingly used in FDM printing technologies to achieve better mechanical, optical, thermal and electrical properties compared to pure polymers. Carbon fibre, glass fibre, Kevlar, wood, metal powder, etc. use as fillers in such materials. Reinforcing filaments for 3D printing with continuous fibres has become possible through the use of special printers with two nozzles: one with matrix polymer, the other with continuous fibre[24, 31].
When composite filament is used for printing, the technology used to produce it has a significant impact on the physical and mechanical properties of the printed part[28]. Heating the fibre before inserting it into the printer nozzle and using prepregs for printing help to increase the degree of fibre impregnation with the matrix material and thus improve the mechanical properties of the finished product[33-36].
3.2. CAD model preparation methods
CAD model preparation consists of design a three-dimensional model of the future part using computer-aided design systems, saving the geometry in STL format and slicing it into layers using special software called a Slicer. Most modern slicer software automatically slices the model into layers of uniform height equal to the thickness of the layer selected for printing, depending on the material properties.
To minimize the stair-step effect, the adaptive slicing method is used, a special algorithm that allows the height of the layers to change depending on the presence of inclined planes in the model[37]. The greater the angle of inclination of the surface, the lower the layer height selected by the software during slicing (see Figure 1). Vertical surfaces are assigned the maximum layer height value because they do not require a lot of detail, and using the highest layer height does not affect the appearance, but significantly reduces printing time. Adaptive slicing into layers allows you to significantly improve the surface quality of the final part with a slight increase in printing time, but this algorithm does not work correctly in all slicer programs and often requires manual adjustment.
3.3. Setting printing parameters
As with any process, there are a number of parameters in the FDM printing that have a major impact on print time, quality and the physical and mechanical properties of the printed parts[38-40]. Choosing the right combination of printing parameters allows you to predict and control the characteristics of the future part.
All the FDM printing parameters can be divided into three groups (Figure 3)[3]:
— equipment parameters (extruder nozzle diameter);
— printing parameters due to the rheological properties of the material (chamber temperature, extrusion temperature, table temperature);
— structural printing parameters (printing orientation, raster thickness, raster width, infill, raster gap, etc.).
The relationship between print input and output parameters is complex and non-linear[41]. Obviously, not all process parameters have the same effect on the final result; some process parameters have a greater effect, others a lesser effect[42-62].
The evaluation of the relationship between printing parameters and part properties is usually carried out using specimens whose shape and dimensions are defined by the relevant standards. Mechanical properties such as tensile strength, yield strength, compressive strength, fatigue strength, relative elongation, toughness, porosity, etc. are determined using tensile, flexural, compression and fatigue tests on specimens of pure thermoplastics[3, 52, 53] and composites with a thermoplastic matrix[30, 54].
Most studies focus on a certain range of parameters, which is illustrated by the Ishikawa diagram shown in Figure 4. Table 1 summarizes the research on the effect of printing parameters on the mechanical properties of specimens made from different materials. The table shows the most commonly used materials in FDM printing (including industrially produced materials), but it should be noted that the range of materials used in this technology is much wider.
Analysis of the data in Table 1 shows that the influence of parameters such as nozzle diameter and layer thickness, grid orientation and raster angle, infill density and extrusion temperature on the physical and mechanical properties of the parts have been most widely studied.
Thus, although FDM printing technologies allow a large number of parameters to be set, these parameters must be optimized to print a stable part with the specified properties, and any even minor change in them can lead to significant, not always positive, changes in the mechanical strength and quality of the finished part. For this reason, when selecting printing parameters for real parts, the recommendations of material suppliers, settings embedded in the 3D printer software for a particular material or the printing of test specimens are most often used.
4. Supplementary treatment in the FDM printing process
Recently, there has been an increasing number of studies aimed at improving the properties of printed parts by affecting the material directly in the printing process. From the information gathered to date, these methods can be divided into three groups[30, 63, 64]:
— additional heating of the extruded layer;
— the use of a vacuum chamber for printing;
— applying ultrasonic vibrations to the table or print head of the printer.
4.1. Additional heating of the extruded layer
The essence of this method is to reheat the applied layer to the glass transition temperature before applying the next layer. Heating can be done by various sources: laser, infrared lamps[65-70], using a direct annealing system — special equipment supplied with some models of 3D printers[71]. Re-heating an already applied layer provides improved adhesion between layers and consequently improved strength properties of the final part[30].
The efficiency of reheating depends largely on the power of the applied sources, the orientation of the sources relative to each other, the distance between them and the print speed. On the other hand, the substrate cooling rate depends on the ambient temperature, the nozzle path and the thermal conductivity of the print material. To avoid overheating, a specially designed system is often used to artificially cool the extruded layer before reheating it[66].
4.2. Printing in a vacuum chamber
The use of a vacuum in the print chamber improves print quality by reducing heat transfer from the nozzle, thus providing a smooth and slow reduction in polymer temperature, which improves adhesion between layers[72-74]. For example, when the pressure is reduced from normal atmospheric pressure to 533.4 mmHg, there is a reduction in waviness and surface roughness of the finished part. Reducing the pressure further to 457.2 mmHg increases the tensile strength of the part compared to normal printing conditions.
4.3. Printing with superimposed ultrasonic vibrations
Ultrasonic processing (UP) is an increasingly used part treatment process that can be applied before, during or after printing to improve part quality. To date, several experiments have been carried out to investigate the effects of ultrasound on polymers and composites, and it has been found that ultrasonic vibration during printing improves the surface quality and strength properties of the final part, while reducing the stair-step effect and layer thickness[63, 64].
The above-mentioned methods used during printing have a positive effect in terms of improving the printed parts properties. However, the using of most of them requires the addition to a standard 3D printer of special equipment for heating/cooling the extruded layer (infrared lamps, lasers, direct annealing system), creating a vacuum in the chamber, applying ultrasonic vibrations, etc., which complicates and consequently increases the cost of the equipment, thus negating the main advantage of the FDM printing method — availability.
5. Post-treatment of FDM printed parts
More recently, post-treatment methods applied to the part at the end of the FDM printing process have been increasingly considered as an alternative to finding the optimum combination of printing parameters[23, 28].
Post-treatment methods can be divided into two groups:
— surface post-treatment, which aims to improve the surface quality of the finished part;
— bulk post-treatment, which can improve not only the surface quality but also the physical and mechanical properties of the finished part.
Let us take a brief look at the most widely studied methods of post-treatment of parts after FDM printing.
5.1. Surface post-treatment methods
Currently, the following groups of surface post-treatment methods are used to minimize the stair-step effect and improve the surface quality of the finished part (Figure 5):
— mechanical methods based on the removal of a layer of material from the surface of the finished part (grinding, polishing, sandblasting, water jetting);
— chemical methods based on partial dissolution of the surface of the finished part in a chemically active environment. In this case, the part may either be completely immersed in the solvent or treated with its vapours;
— thermal methods based on repeated partial melting (re-melting) of the surface of the finished part using a heat source. Such a source is most often a laser (laser grinding, polishing, etc.) or a heat gun;
— the deposition of the coating the surface of a finished part to smooth the its surface by filling pores and smoothing out roughness. Coatings are applied by mechanical (epoxy resin, liquid silicone, paints, etc.), physical (physical vapor deposition (PVD)), chemical (chemical vapor deposition (CVD)) and electrochemical methods.
Most mechanical methods, as well as PVD, CVD and electrochemical coating methods, require special industrial equipment (cutting machines, vacuum equipment, etc.), and mechanical coating of the finished part surface does not usually change the physical and mechanical properties, but only improves the appearance. Therefore, most of the modern research is focused on chemical and thermal (laser) methods of surface post-treatment. Let us highlight some aspects of these methods.
5.1.1. Chemical surface treatment
Chemical surface treatment involves immersing the printed part in a solvent or treating it with hot or cold solvent vapors. Solvents such as acetone, ethyl acetate, tetrahydrofuran, chloroform, dichloromethane, etc. are used[11, 16, 29, 75]. The outer surface of the product is dissolved, the roughness of the surface is smoothed, the gaps between the layers are filled with dissolved polymer. When hardened, the surface becomes smoother. However, a number of studies show that this treatment can adversely affect the mechanical properties of ABS parts[76-78].
5.1.2. Heat treatment
Laser heat treatment is used to reduce the surface roughness of printed parts by rapidly heating and melting the surface of the part. This process smoothes surface irregularities and the molten polymer fills voids in the surface layers to improve physical and mechanical properties[24, 79]. However, a number of studies have found that laser treatment has a greater effect on parts made from semi-crystalline thermoplastics (e.g. PLA), while parts printed from amorphous thermoplastics (ABS and others) show virtually no change in surface roughness[80, 81].
The use of a heat gun as a surface heating source to reduce the porosity of a vacuum system element produced by FDM printing is described[82]. It is found that surface heat treatment with a heat gun at 400 °C combined with 98% infill printing provides a porosity reduction without causing significant deformation, which is particularly relevant for a real part.
In addition to those discussed above, various combinations of surface post-treatment methods are currently used, e.g. combination of acetone vapor treatment with annealing[83], electrochemical polishing, laser ablation with directional (selective) remelting, etc[29]. Most of these methods aim to improve the surface quality of the finished part by smoothing out the stair-step effect. The slight improvement in physical and mechanical properties observed in a number of studies after such treatment is most likely due to the fact that the molten polymer fills voids in the surface layers, reducing porosity and improving interlayer adhesion.
5.2. Bulk post-treatment
Methods that improve the physical and mechanical properties of the printed part include bulk post-treatment methods based on the effect on the whole product, not just the surface.
It is well known that during printing between polymer layers under the influence of temperature and pressure, the interface is heated, resulting in localized polymer flow and molecular mobility (surface contact), the emergence of close physical contact between the two interfaces (so-called neck growth), followed by molecular diffusion of polymer chains across the entire contact area (so-called healing) (Figure 6)[84, 85].
The processes of neck growth and healing are interrelated because molecular diffusion of polymers can only occur in areas where the surfaces are in close contact. The development of such contact depends on the applied pressure, temperature and interaction time, while healing depends mainly on the heating-cooling process and time. Thus the interlayer bond strength σ and consequently the physical and mechanical properties of the part depend on temperature, pressure and treatment time:
During the printing process, the molten filament is fused to the next filament without the application of any additional pressure other than gravity, under non-isothermal conditions and with a very short (on the order of 1 s) interaction time between the layers[84]. Under such conditions, the molecular diffusion process does not have time to develop and the strength of the interlayer bond is low. Additional heating of the filament during printing, as described in the previous section, makes it possible to increase the temperature of the interface and accelerate mutual diffusion throughout the contact zone, resulting in improved physical and mechanical properties of the parts.
Bulk post-treatment allows the process to be carried out under conditions of stable temperature throughout the treatment time, to extend the time of interlayer interaction (from several hours to several days) and to apply additional pressure to the part. This makes the diffusion process through the interlayer interface more efficient and leads to improved physical and mechanical properties.
In terms of the factors that influence the formation of interlayer bonds, all of the bulk post-treatment methods currently used for FDM printed products can be divided into two broad groups (Figure 7):
— methods based on thermal effects on the part (temperature and time factors);
— methods based on both thermal and mechanical effects on the part (temperature, pressure and time factors).
The term annealing (thermal post-treatment) is commonly used for the first group of methods and pressing (hot isostatic pressing (HIP)) for the second group of methods.
5.2.1. Heat post-treatment methods (annealing)
Annealing consists of gently reheating the part to the glass transition temperature of the material or slightly above but below the melting point, holding at the set temperature for a set time and then allowing it to cool naturally to ambient temperature. Repeated isothermal heating, prolonged holding at temperatures near or above the glass transition temperature, followed by slow cooling, ensures sufficient fluidity of the polymer chains, stimulates molecular diffusion across the interlayer interface, increases the number of crystalline structures in the polymer and redistributes stresses within the part, resulting in increased crystallinity and strength[86-88]. It has also been observed that thermal annealing increases the interlayer viscosity of polymers, improving their properties compared to injection molded specimens[89].
A classification of annealing methods has been developed based on the analysis of current research on heat post-treatment (see Figure 7):
— annealing without deformations limitation, where the part is placed in the furnace without size fixation. Heating, holding at a given temperature and cooling can be either single or multi-stage (single or multi-stage annealing);
— annealing with deformations limitation, where special methods are used to fix the part in size: dispersed environment, rigid form or elastic shell.
Table 2 describes the studies on annealing methods. The studies are grouped according to the given classification of methods and according to the type of material — amorphous and semi-crystalline thermoplastics and composites based on them, since the mechanisms and the degree of influence of heat post-treatment depend largely on the material of the filament used for printing.
5.2.1.1. Annealing without deformations limitation
The essence of annealing without deformations limitation is that the part is placed freely in the furnace and is not fixed in any way. The influence of annealing temperature, heating and cooling time on the physical and mechanical properties of parts made from pure thermoplastics and composites based on them is considered. The most commonly used amorphous thermoplastics for FDM printing are PEI and ABS. Heat treatment of parts made from these materials above the glass transition temperature results in a significant reduction in surface roughness and stair-step effect and contributes to an improvement in physical and mechanical properties (tensile, compressive, bending and impact strength)[90]. Heat post-treatment of thermoplastic polyurethane (TPU) parts effectively reduces porosity, increases interlayer contact area and, consequently, structural density, tensile strength and relative elongation[91]. The authors also note that after heat treatment, the water resistance of the products is significantly improved and the wetting angle increases. In most of the studies carried out on parts made of amorphous thermoplastics, the improvement in physical and mechanical properties is explained by the repeated partial melting of the material during annealing, which leads to a reduction in porosity and interlayer gaps and improves the diffusion of the material of the different layers.
In the heat treatment of semi-crystalline thermoplastics, the annealing temperature is more important for improving the physical and mechanical properties and the holding time at a given temperature is less important. Annealing in the range between the glass transition temperature and the melting temperature of a given polymer promotes an increase in the degree of crystallinity, resulting in an improvement in strength properties. As the temperature increases further, the effects of polymer chain degradation begin to dominate, the degree of crystallinity decreases and the strength properties deteriorate.
The most commonly used semi-crystalline thermoplastic in FDM printing technologies is PLA, which has a glass transition temperature in the range of 60 – 65 °C. Annealing PLA parts at temperatures above the glass transition temperature increases the degree of crystallinity and interlayer diffusion, thereby improving physical and mechanical properties such as tensile strength, Young’s modulus, Shore hardness and flexural stress[92-97]. At the same time, increasing the holding time does not have a significant effect on the physical and mechanical properties, as it is not sufficient to achieve the maximum degree of crystallinity[94]. A comparison of the annealing results of PLA and ABS specimens shows that semi-crystalline PLA parts show an increase in tensile strength after annealing, while amorphous ABS products show significantly poorer tensile test results[86]. Studies conducted for other semi-crystalline materials (polypropylene[98], PC-ABS[99]) confirm the fact that heat post-treatment in the range of temperatures above the glass transition temperature but below the melting point improves physical and mechanical properties by increasing the degree of crystallinity (usually up to 20 – 30%)[96, 98, 99]. However, increasing the annealing time does not lead to further structural changes or improvement of properties. In addition, further increase of the annealing temperature and, as a consequence, increase of the degree of crystallinity above 50% may lead to embrittlement of the material and deterioration of the physical and mechanical properties of the part.
Annealing of composite printed parts also significantly improves their physical and mechanical properties — tensile strength[100], hardness, flexural strength[101-103]. Heat post-treatment increases toughness and reduces internal stresses[101]. And after annealing, composite parts have better strength properties than pure polymer printed parts. The properties of heat post-treated composite parts are directly related to the conditions under which the composite was produced and the amount of filler in the composite[102]. The improvement in physical-mechanical properties is a consequence of the reduction in the number of pores and the higher interlayer adhesion obtained by annealing, as well as the reduction in the gaps between the fibres and the polymer[101, 102].The dependence of the physical-mechanical properties of annealed parts on the degree of crystallinity and the deterioration in strength properties at higher annealing temperatures observed for pure polymers are also typical for composites based on them[103].
Heat post-treatment can be carried out using special equipment (vacuum furnace) that maintains the vacuum throughout the annealing process[103]. Heat post-treatment carried out under vacuum conditions makes it possible to increase the strength and reduce the porosity of parts printed from composite materials based on semi-crystalline matrices by increasing the degree of crystallinity of the matrix material and the formation of cross-layer molecular chains. In addition, such post-treatment makes it possible to change the mode of product fracture from the predominant delamination at the ‘matrix-fibre’ surfaces observed in untreated parts to fracture at the surfaces of the printed layers in vacuum-treated parts[104]. However, to date there are very few studies of vacuum annealing, and the use of specialized equipment for post-treatment is not always possible.
Heat treatment carried out without fixing the dimensions of the parts improves their physical and mechanical properties, but causes unacceptable deformations that may render the part unusable[83, 100, 102, 105-107]. This is due to the fact that in an unfixed part there are no forces preventing its expansion at high temperatures, and on cooling the inhomogeneous temperature distribution causes bulk shrinkage and the formation of residual stresses. In addition, composite parts have lower elongation values than pure polymers, depending on the filler content and the type of post-treatment[83, 102].
In order to minimize deformation during the heat treatment, it is possible to carry out annealing under conditions where the specified temperature is reached in several stages (multi-stage or cyclic annealing)[104]. To treat PLA specimens at a specified annealing temperature of 110 °C, it was proposed to heat the parts in 3 stages: in the first stage, the parts were heated to 70 °C and cooled to 50 °C after 10 minutes; in the second stage, they were heated to 90 °C and cooled to 50 °C after 10 minutes; in the third stage, they were heated to 110 °C and cooled to 50 °C after 10 minutes. According to the authors, the cyclic annealing technology reduces shrinkage by up to 50% and improves the strength properties of the parts (compressive and impact strength) compared to conventional annealing.
Obviously, at a different annealing temperature, the sequence and duration of the heating, cooling and holding stages will be different. Therefore, for each material it is necessary to develop its own algorithm of ‘heating – cooling – heating – holding’, as well as the selection of specific temperatures and times for different stages. Nevertheless, the technology of multi-stage annealing can be considered as an alternative to traditional single-stage annealing, contributing to a significant reduction in deformation during the annealing process.
5.2.1.2. Annealing with deformations limitation
Recently, many studies have proposed different technological methods to limit the deformation of parts during heat post-treatment: annealing in a dispersed environment, in a rigid form or in an elastic shell. Let us take a closer look at the annealing methods that make it possible to limit the deformation of parts during heat treatment.
5.2.1.2.1. Annealing in a dispersed environment
environment consists of easily dispersible materials that do not complicate subsequent cleaning — common salt, gypsum, talc, sand, aluminium oxide. The dispersed environment in the closed container allows the part to be fixed in all axes and also acts as a heat insulator. Obviously, the material used as a environment has an additional influence on the magnitude of deformations in the annealing process.
The use of aluminium oxide powder Al2O3 during annealing allows a significant reduction in deformation of both amorphous and semi-crystalline thermoplastic parts compared to annealing without deformations limitation[105, 106]. A decrease in deformation is observed with increasing annealing temperature. However, the researchers note that the use of fixing the parts in a dispersed material during annealing does not have a significant effect on their properties and only contributes to the reduction of deformations.
Sodium chloride is the most preferred material for dimensional fixation of parts in terms of environmental friendliness, cost, ease of dispersion and subsequent cleaning. The use of NaCl powder increases the tensile and compressive strength of parts made of various thermoplastics (PETG, PLA) compared to untreated ones[87, 88]. The improvement in the physical and mechanical properties of annealed parts is explained by a higher interlayer diffusion of the material, which is confirmed by studies of the internal structure using a scanning electron microscope[87].
Compared to parts treated with common salt powder, products treated with CaSO4 gypsum show an increase in average hardness, microhardness and tensile strength[88]. Both materials reduce the plasticity of the parts, making them more brittle. Annealing in sand gives minimal improvement in the properties of the parts compared to untreated parts[107]. Studies on the deformation of parts post-treated in different environment also show a preference for the use of gypsum as a dispersed environment. For example, products annealed in gypsum show minimal deformation compared to those annealed in sand[107].
Figure 8, Figure 9 and Figure 10 show examples of heat post-treatment in various dispersions.
In some works, an additional pressure on the dispersed environment is used[87, 108]. The pressure can be created by means of a lid or additional weights and can be up to 1 MPa (Figure 11)[108]. The application of this technology not only allows to improve the physical and mechanical properties of the parts (porosity, tensile strength), but also contributes to a significant reduction in the anisotropy of properties typical for the FDM printed parts[108]. This is easily explained in terms of the interlayer bonding mechanism described above, as a third factor, pressure, is added to the two factors (temperature and time) characteristic of most annealing techniques.
A comparison of the results of heat post-treatment of parts carried out in dispersed environment of different compositions shows that gypsum is the most preferred material from the point of view of achieving the best physical and mechanical characteristics of annealed parts and reducing their deformations during annealing. This is explained by its higher heat resistance and hardness compared to other materials used to prevent compression and expansion of the part during heat treatment[88, 107].
Post-treatment in a dispersive environment, combined with the choice of printing parameters, can also significantly improve the physical and mechanical properties of parts made from different materials. For example, parts printed in a vertical orientation (usually the lowest strength) and then annealed in NaCl powder have better mechanical properties than those printed in a horizontal orientation but not annealed[87]. The greatest increase in tensile strength is obtained when parts printed with a raster angle of 0°/90° are treated in gypsum, and the greatest increase in microhardness is obtained in parts with a raster angle of –45°/45°[88]. Treatment in a dispersed environment with additional pressure enhances the effect of post-treatment both in terms of improving physical and mechanical properties and reducing part deformation.
Thus, from the point of view of reducing part deformation, treatment in a dispersed environment gives better results than unfixed parts, while achieving approximately the same improvement in physical and mechanical properties. However, to date, the literature does not provide clear recommendations on the choice of one or other type of annealing environmen, nor does it practically address the issue of cleaning the parts after immersion in a dispersed environmen, which is particularly relevant when applying this technology to complex geometric shape parts.
5.2.1.2.2. Annealing in rigid form
Rigid form (mold) annealing is carried out in special molds, similar to injection molds or casting forms. The internal surface of the mold is a negative replica of the part shape and fixes the part in all planes during annealing. The molds are usually made of aluminium or its alloys. Heat treatment of parts made of thermoplastics and composites based on them, carried out in such molds, makes it possible to increase the tensile strength and relative elongation of the products, while the orientation of the imprint does not significantly affect the mechanical properties[109]. The use of metal molds allows not only annealing but also melting (heating above the melting point) to be used as a treatment. Melting heat treatment applied in combination with print orientation can significantly improve tensile strength[109].
A variant of the combined effect is the use of a negative of the shape of the part mold, to which additional pressure is applied using a plate shaped to the shape of the part (Figure 12)[110]. This combination of influences makes it possible to improve the physical and mechanical properties of the parts, not only in comparison with untreated parts, but also in comparison with those treated in a dispersed environment, since the addition of the third factor — pressure — has a positive effect on the process of interlayer bonding. Although there are deformations of the parts during annealing in a pressured mold, they are much smaller than those during annealing in a dispersed environment[110].
Obviously, from the point of view of limiting deformation, a rigid form representing a negative replica of the part shape is the most reliable way of fixing dimensions. However, specimens for different types of strength tests and studies of other properties often have different geometric shapes, regulated by the relevant requirements (blades, plates, cubes). In other words, for complex property studies, it is necessary to have a several molds or a multi-seat mold that allows specimens with different geometries to be treated simultaneously. In the case of post-treatment of real parts, it will be necessary to design and manufacture molds for annealing, similar to injection molds, which is a time-consuming and expensive process.
5.2.1.2.3. Annealing in an elastic shell
Annealing in an elastic shell consists of placing the part in an elastic shell, such as a polyamide bag, in order to fix its dimensions during post-treatment[111, 112]. To reduce the gap between the shell and the part and to better fix the part before it is placed in the oven, the air is pumped out (Figure 13).
Parts annealed in an elastic shell, have higher tensile strength, Young’s modulus and bending strength, as well as lower surface roughness and porosity than parts annealed without dimensional fixation[111, 112]. However, significant part deformation is observed during treatment in an elastic shell compared to treatment in a dispersed environment, which may be due to the lack of complete sealing of the part during heating-cooling[112]. It is suggested that the air be pumped out throughout the heat treatment process and that other types of elastic shells be investigated as a solution to the problem.
Thus, heat post-treatment technologies with deformation limitations give significantly better results in terms of part dimensional distortion compared to annealing with free deformation. However, at present there are no systematic studies on the influence of this or that method of deformation limitation on the properties of the parts, and there is practically no report on the application of these technologies to real complex shapes parts obtained by FDM printing.
Analysis of literature shows that annealing contributes to significant improvement of physical and mechanical properties and surface quality of FDM printed parts. Comparison of the effect of different post-treatment methods on surface quality, dimensional accuracy and mechanical properties of parts shows that annealing is more effective than surface treatment in terms of improving both physical and mechanical properties and surface quality for parts printed from the same material.
5.2.2. Methods based on the action of both heat and mechanical forces (pressing)
Isostatic pressing is a process in which the same pressure is applied to the workpiece in all directions to improve the homogeneity and microstructure of the workpiece material without the geometric constraints inherent in uniaxial pressing. Isostatic pressing is most commonly used to reduce porosity in metals and ceramics. Since the nature of FDM printing is based on layer-by-layer deposition of material, the application of this type of pressing should have a similar effect of improving interfacial bonding between layers. Therefore, a number of recent publications have proposed a method based on the application of high temperature combined with high pressure to the specimen as an alternative to the traditional annealing of FDM printing parts[113-119]. In analogy to the existing manufacturing process used for densification of metals and ceramics, this group of methods has been named hot isostatic pressing (HIP).
HIP technology involves placing the part in a hermetically sealed container (autoclave) filled with gas (argon, helium or nitrogen). The part is subjected to isotropic compression under high pressure (approximately 2 – 5 MPa) at a temperature close to the melting point of the material. Since, as mentioned above, the molecular diffusion of the polymer at the interlayer interface is temperature and pressure dependent, it is difficult to achieve effective polymer diffusion under annealing conditions based on the application of elevated temperatures alone. Therefore, the addition of a third factor, pressure, is necessary to further improve the interlayer bond strength. The application of isostatic pressure promotes the formation of a denser and wider interlayer contact and the heating of the interface almost to melting point. Thus, hot isostatic pressing increases the interlayer bond strength through polymer diffusion, reduces the number of voids in the microstructure, and consequently improves the physical and mechanical properties[118-120].
The analysis of publications allowed us to develop a classification of pressing methods, analogous to the classification of annealing methods (see Figure 7):
— pressing without deformations limitation, when the part is placed in the autoclave without fixing;
— pressing with deformations limitation, when special means — dispersed environment or elastic shell — are used to fix the product by its dimensions.
Table 3 summaries the studies carried out for the HIP methods. As we see from Table 3, research is currently being carried out mainly on polyamide-based composites and some types of high-performance thermoplastics.
5.2.2.1. Pressing without deformations limitation
The technology of pressing without deformations limitation consists in placing the part in a special container (autoclave), into which gas is injected by means of a compressor until the set pressure is reached, and then the container is heated to the set temperature. The lower limit of the temperature is the glass transition temperature of the polymer being tested, the upper limit, which ensures minimal part deformation, is the heat deflection temperature (the temperature at which the polymer specimen retains its rigidity and shape under constant load). The part is kept at the set temperature and pressure throughout the treatment and then slowly cooled to ambient temperature.
The results of the research clearly show that treatment by isostatic pressing technology significantly improves the mechanical properties of FDM parts: increased tensile, shear and bending strength, reduced porosity, increased degree of crystallinity.114 – 116
The authors of the study attribute this improvement in mechanical properties primarily to the combined effects of elevated temperature and pressure, resulting in a denser interlayer interaction that fills voids and closes cracks created during the printing process.114 – 115
The increase in the degree of crystallinity under HIP conditions is explained by the fact that the crystallization process proceeds faster at higher temperatures and pressures, which contributes to the acceleration of the polymer crystallization process and an increase in the number of crystals. In addition, since the matrix and filler are in closer contact under isostatic pressure conditions, the filler fibres can play the role of nucleation centers and also contribute to an increase in the number of crystals.114 – 116
5.2.2.2. Pressing with deformations limitation
Due to the small number of studies on the application of isostatic pressing technology after FDM printing, there is virtually no data on part deformation after post-treatment. Only paper 116 notes significant deformations after HIP, caused by possible fibre reorientation under high pressure conditions, and recommends further research to identify the influence of post-treatment process parameters, including on part deformations. At present, however, a number of papers have been published in which isostatic pressing is carried out under conditions where the part placed in the autoclave is additionally fixed in one way or another. By analogy with annealing technologies, a dispersed environment 117 or an elastic shell (polyamide bag) can be used to fix the part.118, 119
5.2.2.2.1. Pressing in dispersed environment
Dispersed environment pressing consists of placing the part in a container filled with a finely dispersed substance. A gas is pressurised into the container until a set pressure is reached, after which the container is heated to a set temperature. Since the pressure is not applied directly to the part but is redistributed through the environment, the treatment process is called ‘quasi-isostatic pressing’.117 Currently, only NaCl is considered as a dispersed environment. The effect of temperature, pressure and processing time on the physical and mechanical properties of thin-walled parts has been studied. It has been found that as the temperature and processing time are increased, the compressive strength increases, and the application of pressure allows the strength and impact resistance of thin-walled structures to be increased simultaneously. It has also been found that treatment in a dispersed environment gives a more uniform deformation of the parts compared to pressing without deformations limitation.
5.2.2.2.2. Pressing in an elastic shell
Elastic shell pressing consists of placing the part in a polyamide bag from which air is pumped out to reduce the internal pressure and gap. The part is then placed in an autoclave where it is treated using the HIP technology described above. At present, studies of this technology have been carried out by the authors of Refs 118, 119 for parts made of composite material based on polyamide-12 filled with carbon fibre. As the studies were carried out at temperatures well below the melting point of the matrix material, the authors refer to this technology as warm isostatic pressing (WIP). The tendency to improve the physical and mechanical properties (strength and impact resistance) and to increase the degree of crystallinity of parts made of composite materials based on polyamide matrix, which is characteristic of hot isostatic pressing, is also observed for WIP technology. The use of an elastic shell in combination with air evacuation promotes the redistribution of internal and external pressures in the part, increases the strength of the interface between the layers and improves the interlayer diffusion of the polymer, which in turn leads to a significant improvement (in the order of 1.5 to 2 times) in the physical and mechanical properties compared to parts treated without the polyamide shell.118 However, the authors note the presence of significant parts deformations of the due to the application of high pressure, which is unacceptable in the case of post-treatment of parts with complex shapes or thin-walled elements. In addition, despite the positive effect of the elastic shell, there are obvious limitations to its use, as the polyamide currently used for production has low temperature resistance. For post-treatment of parts made of materials with high glass transition and melting points, suitable alternative materials for elastic shells must be selected.
Thus, the technology of hot isostatic pressing makes it possible to significantly improve the physical and mechanical properties of FDM parts printed from composite materials, bringing them closer to the properties of parts made by injection molding. However, this technology requires the use of special equipment — an autoclave with the possibility of pressure and temperature control, which is possible and justified in the conditions of large industrial enterprises producing large batches of products, and practically impossible in the conditions of small research laboratories and small enterprises. In addition, HIP technology is currently poorly understood, both in terms of the multiphysical phenomena governing the relationship between the internal structure, post-treatment parameters and properties of the final product, and in terms of predicting the residual deformations of real parts.
Based on the analysis of research in the field of supplementary treatment, we have formulated recommendations for the choice of post-treatment method for real FDM printed parts, depending on the requirements placed on them (Table 4). According to Table 4, to improve the physical and mechanical properties of real FDM printed parts, including complex geometric shapes, the most promising methods, which do not require the use of special or expensive equipment, are chemical post-treatment of the surface, multi-stage annealing and annealing in an elastic shell (green boxes in Table 4).
6. Conclusion
In recent years, FDM printing has been increasingly used in various branches of production and science for the manufacture of products of complex geometry from a wide range of thermoplastic materials and composites based on them, and is considered as a technology competing with injection molding. The choice of optimal process parameters and supplementary treatment during printing allow only partial elimination of defects in the finished product caused by the specificity of the FDM printing process. Therefore, the attention of researchers is increasingly focused on the search for post-treatment methods aimed at improving the mechanical properties and surface quality of FDM printing parts. The analysis of publications carried out during the preparation of this review has shown that, to date, there is practically no complete and clear description of methods for the supplementary treatment of parts obtained by FDM printing.
The review proposes a classification of supplementary treatment methods for FDM printing parts, including pre-printing preparation, supplementary treatment directly in the printing process and treatment after the part has been printed, and a classification of heat post-treatment methods based on heat (annealing) and heat and mechanical (pressing) effects on the part. The classifications are one of the first attempts to systematize current research in the field of supplementary treatment.
Analysis of modern research has shown that, since the strength of the interlayer boundary and, consequently, the physical and mechanical properties depend on temperature, pressure and processing time, bulk post-treatment based on prolonged isothermal exposure and pressure allows the process of material diffusion through the interlayer boundary to be made more efficient, leading to an improvement in the physical and mechanical part properties. Annealing, based on the effect of temperature on the part, makes it possible to obtain physical and mechanical properties comparable to those of parts obtained by injection molding. Different technological methods can be used to minimize the deformation observed after heat treatment (annealing in a dispersed environment, a rigid form or an elastic shell). Pressing using temperature and pressure can significantly improve the physical and mechanical properties of FDM printed parts compared to traditional annealing. This is due to more efficient interlayer diffusion of the polymer and an increase in the degree of crystallinity. However, the widespread use of this method is limited by the need for specialized equipment, which is practically impossible for small research laboratories and small companies.
Based on the analysis of research in the field of supplementary treatment, the review formulates recommendations on the choice of post-treatment method for real FDM printed parts depending on their requirements.
According to the authors of the review, the development of research in the field of supplementary treatment of FDM printed parts can take several directions: widening the range of materials studied, especially composites; searching for new and improving already developed methods aimed at minimizing deformation of real parts both after annealing and after pressing; accumulating real material describing the relationship between post-treatment parameters and physical and mechanical properties of parts; conducting studies on the effects of post-treatment not only on test specimens but also on real parts with geometrical and technical requirements; extending studies on the molecular diffusion process (including the development of mathematical models) both during printing and post-treatment.
All this will make it possible in the future to complete the classification of post-treatment methods proposed by the authors of the review and to develop recommendations for the choice of post-treatment method for FDM printed parts, depending on their shape and requirements, not only on the basis of experimental data but also on the basis of computer modeling.
7. List of abbreviations
ABS — acrylonitrile – butadiene – styrene copolymer;
ASA — acrylonitrile – styrene – acrylate copolymer;
AM — additive manufacturing;
CAD — computer-aided design;
CF — carbon fiber;
CVD — chemical vapor deposition;
FDM — fused-deposition modeling;
FGF — fused granulate fabrication;
GF — glass fiber;
HIP — hot isostatic pressing;
KF — kevlar (fiber);
PA — polyamide;
PA6 — polyamide-6;
PC — polycarbonate;
PEEK — polyether ether ketone;
PEI — polyetherimide;
PEKK — polyether keton ketone;
PET — polyethylene terephthalate;
PETG — glycol-modified polyethylene terephthalate;
PLA — polylactide;
PP — polypropylene;
PPS — polyphenylene sulfide;
PVD — physical vapor deposition;
TPU — thermoplastic polyurethane;
UP — ultrasonic processing;
UV — ultrasonic vibration;
WIP — warm isostatic pressing.
Acknowledgements
The research was carried out with the financial support of the Committee for Science and Innovation of Tula Region under the agreement No. 10 dated 07.09.2022.
References
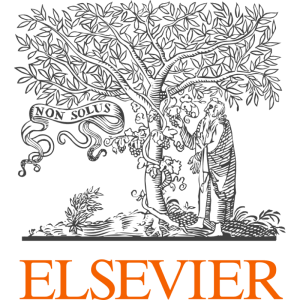
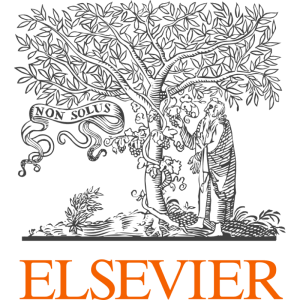
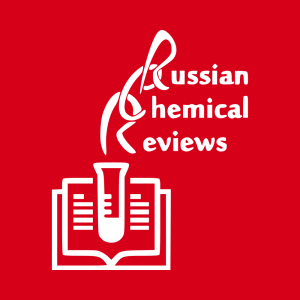
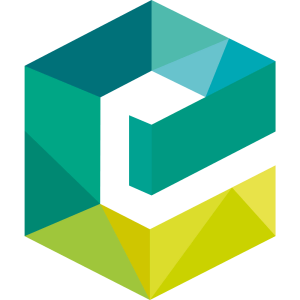
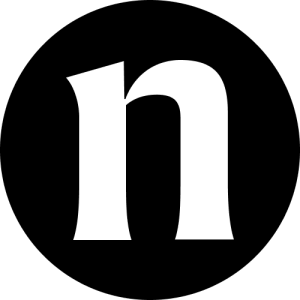
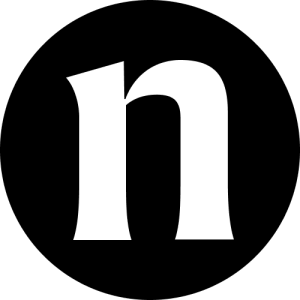
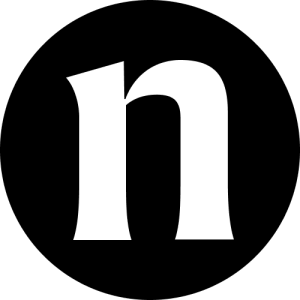
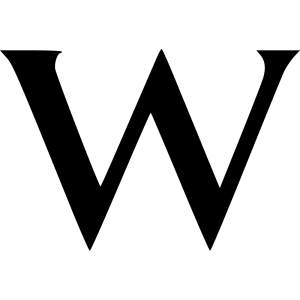
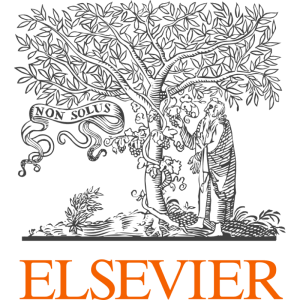
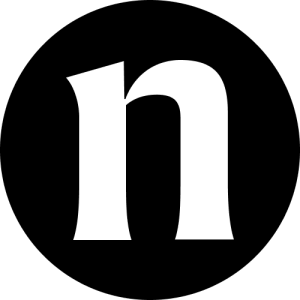

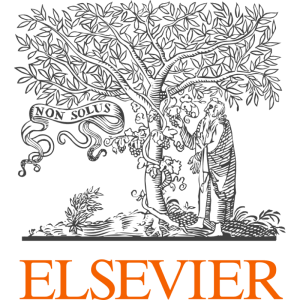

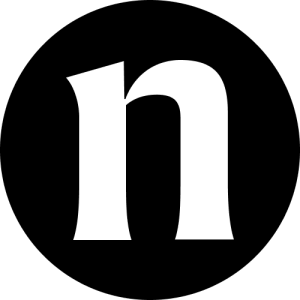
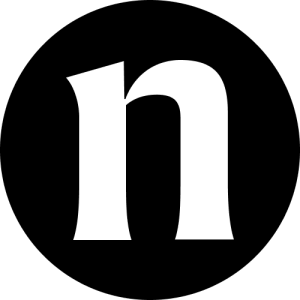

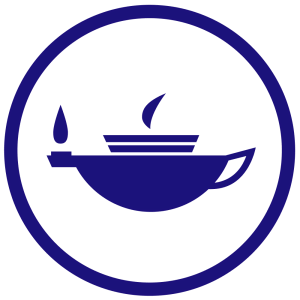

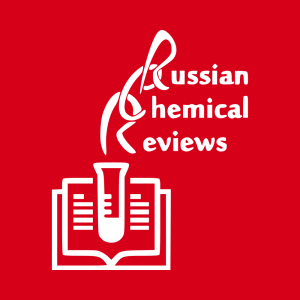
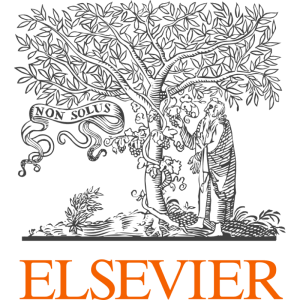

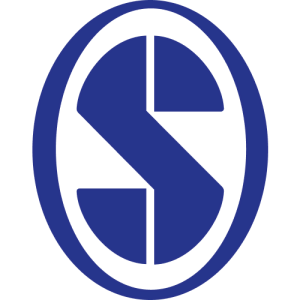
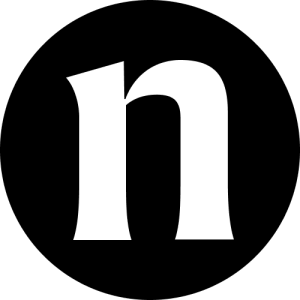

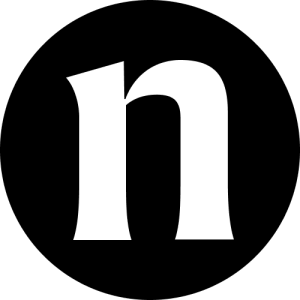
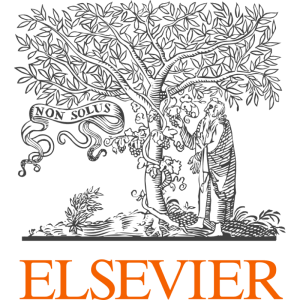
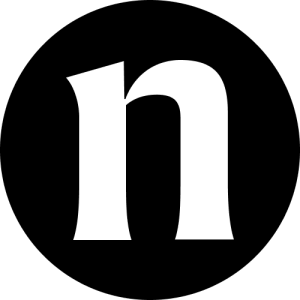
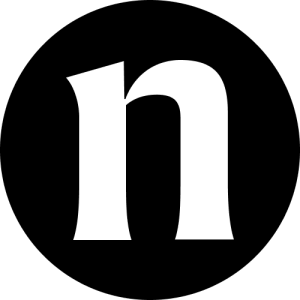
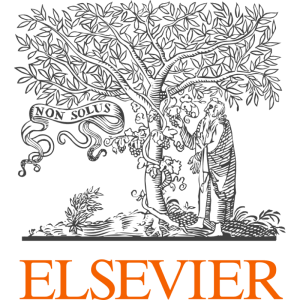
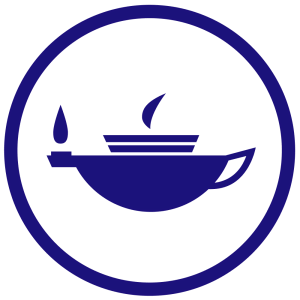
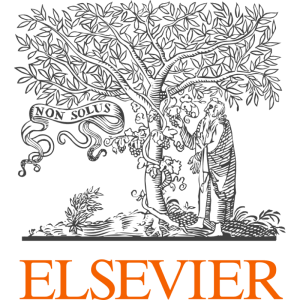
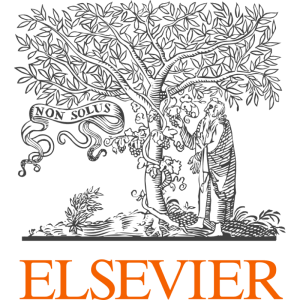

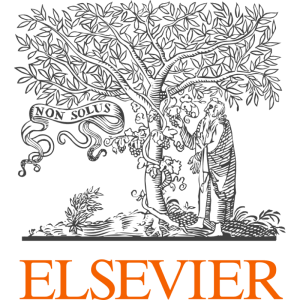
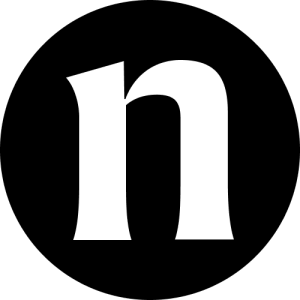
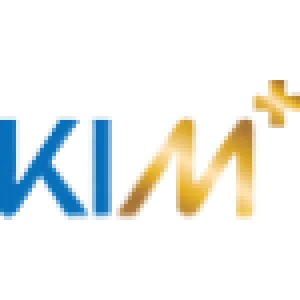
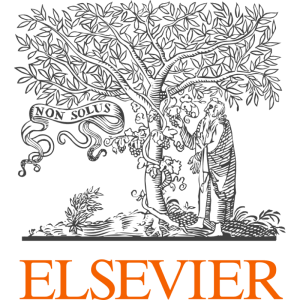
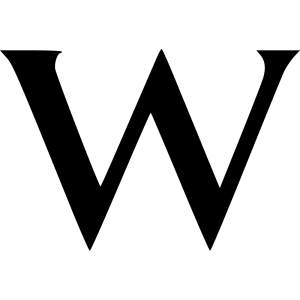
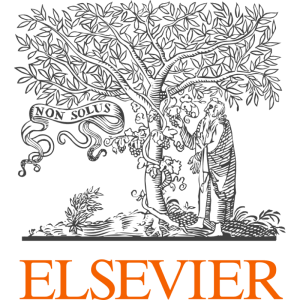
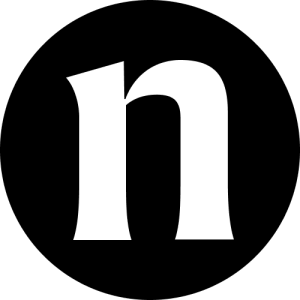
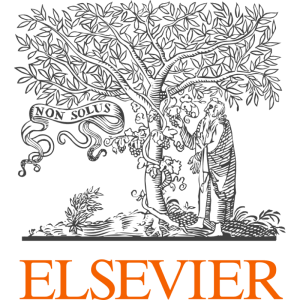
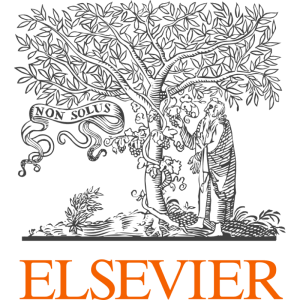
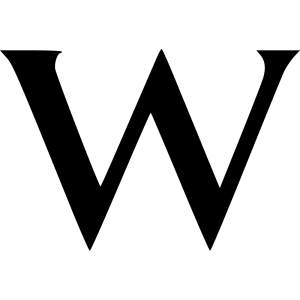
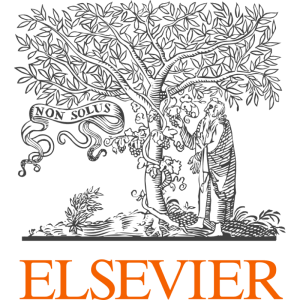
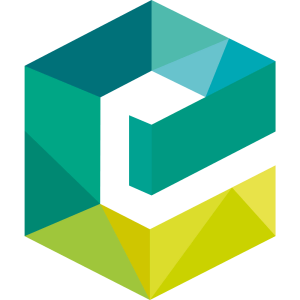
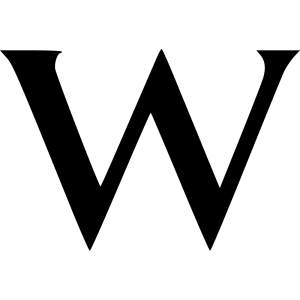
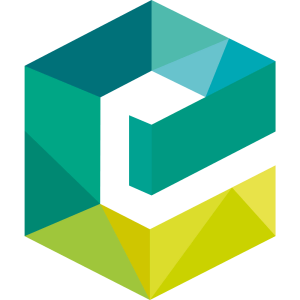
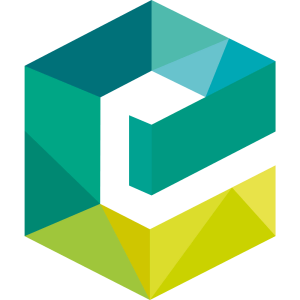
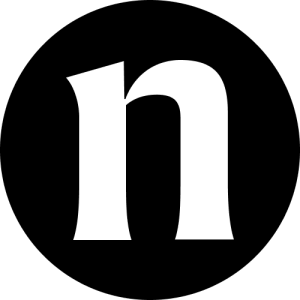
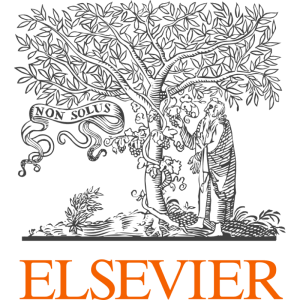

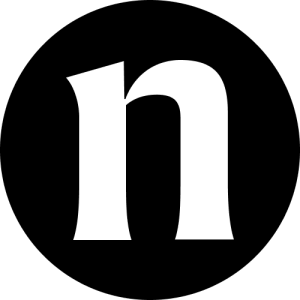


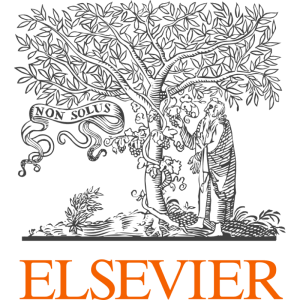
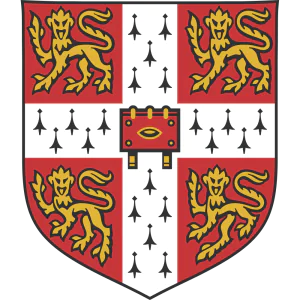
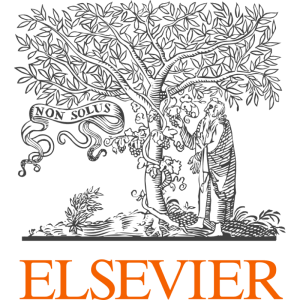
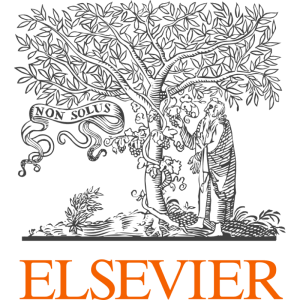
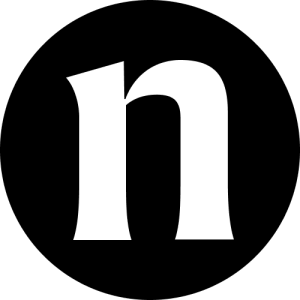
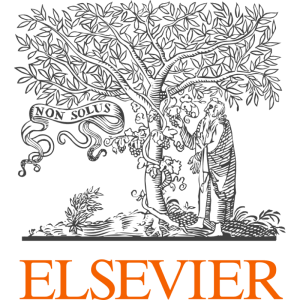
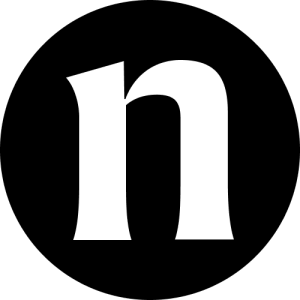
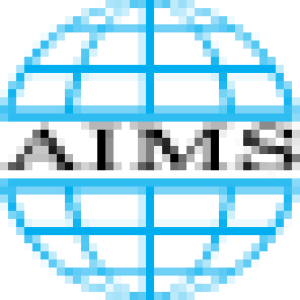
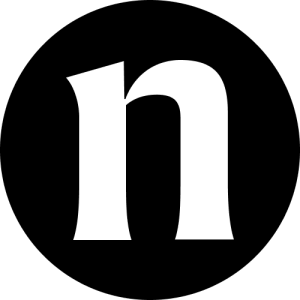
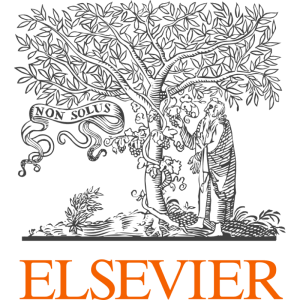
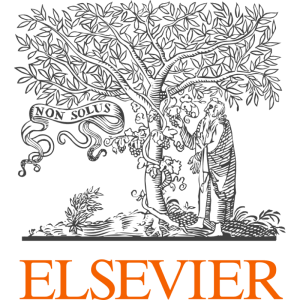
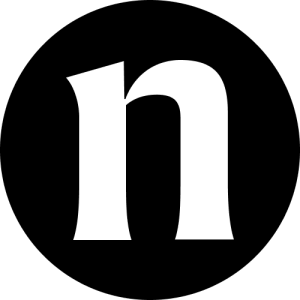


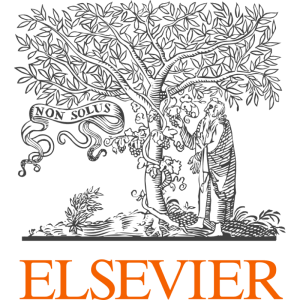
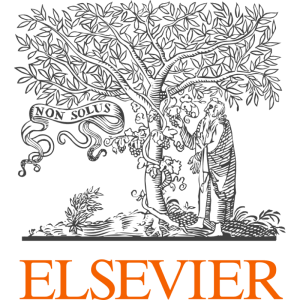
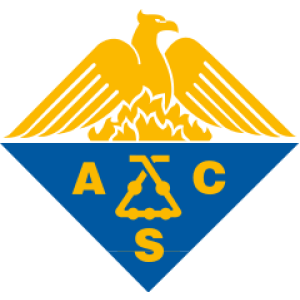


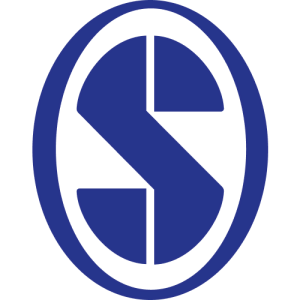
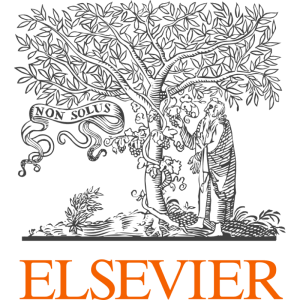
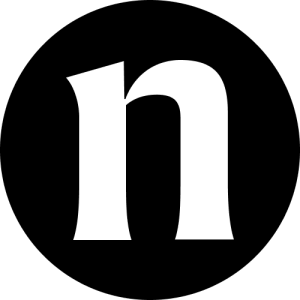
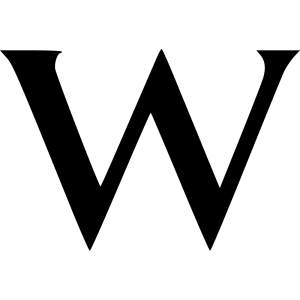
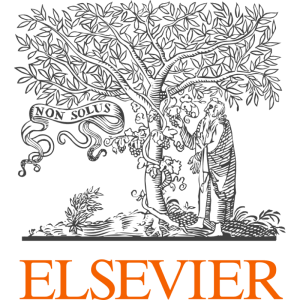
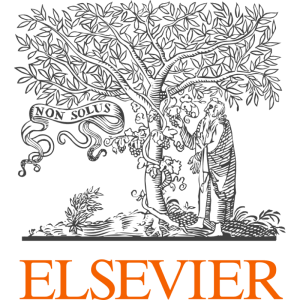
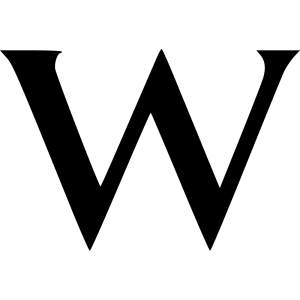
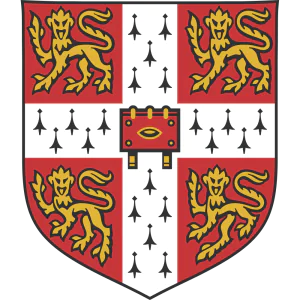
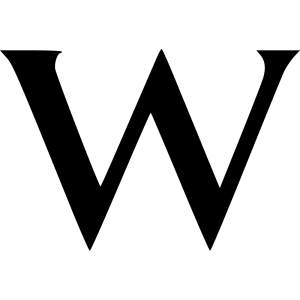

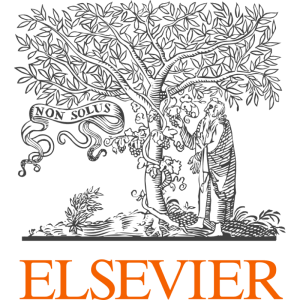

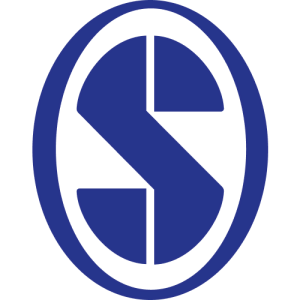



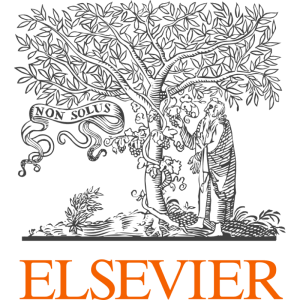
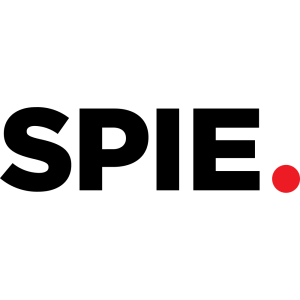
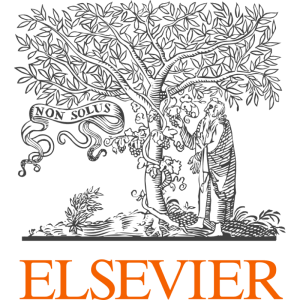
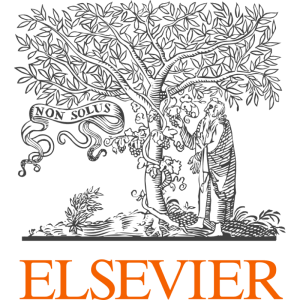
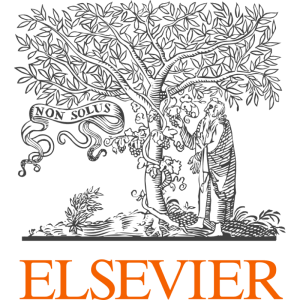
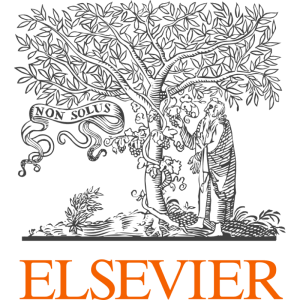
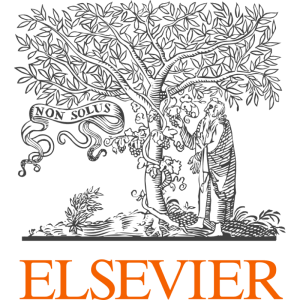
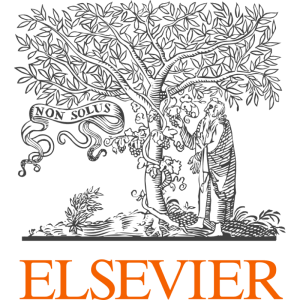
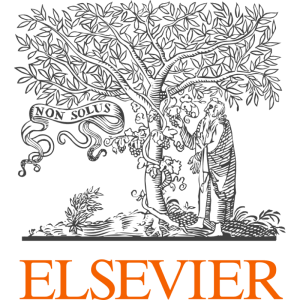
